- Services
- Condition Monitoring and Machinery Diagnostic…
Condition Monitoring Services
A high degree of precision and efficiency is vital for sophisticated rotating and reciprocating devices for they have to work 24*7 throughout the year without even a minute calibration error. Technomax offers condition-based maintenance services that will ensure that the installations are working perfectly. We follow the successful condition-based predictive maintenance strategy rather than the calendar-based preventive maintenance program. Our Condition monitoring services support proactive maintenance and production planning, thereby reducing maintenance costs and downtime. By leveraging the experience we’ve gained in the field of condition monitoring and diagnostics, we make sure that you can fully utilize the operational lifetime of the technical components.
How condition monitoring can help you
- Increase the overall installation lifespan.
- Keep high product efficiency throughout.
- Cut down unexpected downtime.
- Plan effective maintenance & inspection.

Our Expertise
Our expertise is spread over almost every service in condition monitoring and diagnosis, and we’ve served several customers of various industries. Reliability engineering services offered by Technomax have been of the highest quality standards. Some of our Condition Monitoring Services include
- Vibration Analysis.
- Infrared Thermography Testing.
- Ultrasound Inspection.
- Alignment and Balancing.
- Machinery Lubrication.
- Fluid Analysis.
Our Services
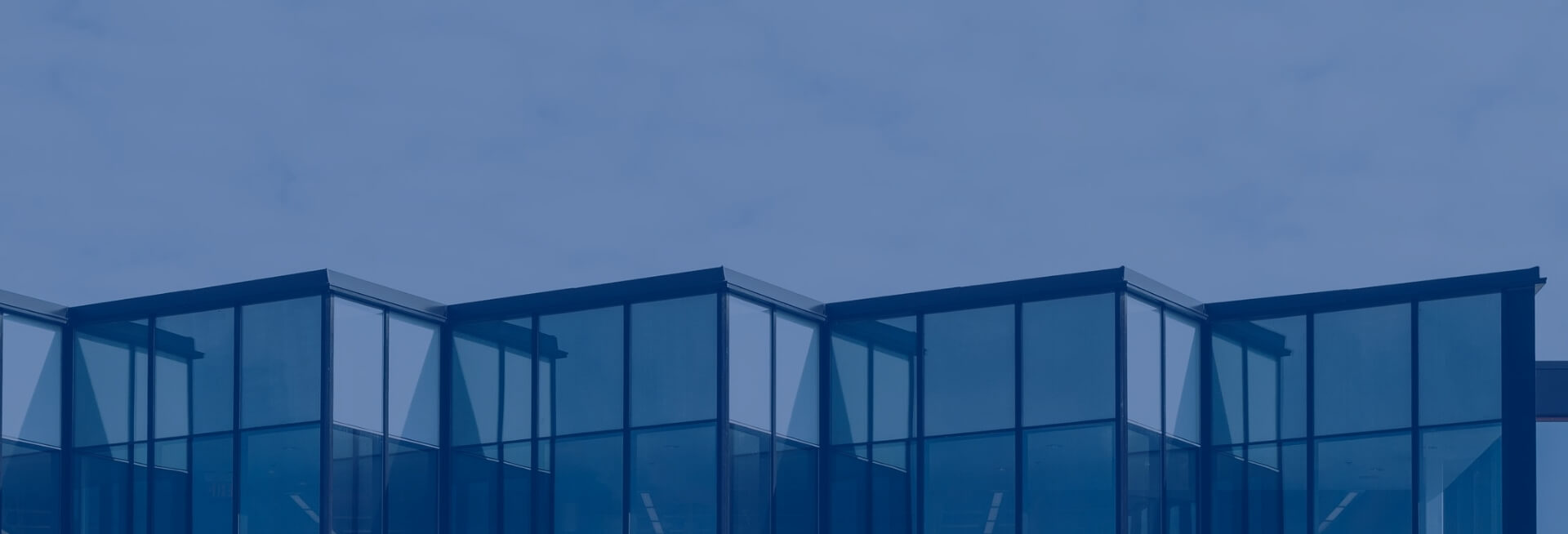
Get Started Now!
It takes less than a minute of your time. Or you may simply call +971 2 555 1 783