- Services
- Advanced Vibration Analysis & Troubleshooting…
Advanced Vibration Analysis & Troubleshooting of Rotating Machinery
The efficient and reliable operation of rotating machinery is crucial in today’s industrial sector for increasing productivity and reducing downtime. Vibration analysis has become an essential technique for evaluating the operation and health of such equipment. Engineers and maintenance specialists may identify and diagnose underlying problems before they develop into expensive failures thanks to this cutting-edge method, which goes beyond the conventional approach.
Key aspects and techniques used in advanced vibration analysis
- Vibration sensors: The first stage in modern vibration analysis is installing top-notch vibration sensors on rotating machinery. These specialized sensors, such as proximity probes and accelerometers, are essential for precisely identifying and measuring vibrations. Engineers and maintenance specialists can spot possible problems and implement effective troubleshooting techniques thanks to these sensors' ability to capture different vibration signal characteristics.
- Data acquisition: A crucial stage of sophisticated vibration analysis is data acquisition. Engineers can continually monitor and record sensor vibration signals using sophisticated data-gathering systems. This data forms the basis for further investigation, providing thorough insights into the condition and functionality of rotating machinery. By utilizing this, professionals can proactively identify probable issues, optimize maintenance plans, and guarantee important equipment's reliable and effective functioning.
- Signal processing: Applying complex algorithms to the collected vibration data makes signal processing crucial in vibration analysis. Analyzers improve the signal-to-noise ratio through filtering, averaging, and other techniques, making it possible to extract important information from raw data. These transformed insights contribute to a greater comprehension of the dynamic behavior of the equipment, exposing hidden patterns and assisting in the early identification of potential defects. These cutting-edge processing techniques enable maintenance specialists to make decisions and perform precise repair operations to guarantee rotating machinery's optimum performance and reliability.
Time-domain analysis:
Time-Domain Analysis, which involves a detailed evaluation of vibration signals in the time domain, is a key technique in vibration analysis. Engineers may learn a lot about the temporal behavior of vibrations by carefully examining patterns, transients, and anomalies. This analysis helps identify particular fault types and enables the early identification of anomalies in rotating machinery. With this information, maintenance specialists can quickly address possible problems, avoiding expensive downtime and guaranteeing the efficient running of critical equipment in various industrial sectors.
Frequency analysis:
Frequency analysis is a key component of sophisticated vibration analysis, which converts vibration signals from the time domain to the frequency domain using methods like the Fast Fourier Transform (FFT). Engineers can then reveal the harmonics and prominent frequencies in the vibrations, among other frequency components. These results serve as helpful markers of certain rotating machinery issues, enabling proactive fault diagnosis and simplifying prompt maintenance interventions to guarantee critical equipment performance in industrial operations. Gearbox vibration analysis is one of the frequency analyses used to find gear faults.
Modal analysis:
ODS and Modal analysis is a vital approach in advanced vibration analysis to determine rotating machinery’s inherent frequencies, mode shapes, and damping characteristics. Engineers are given a thorough insight into the system’s dynamic behavior thanks to this crucial information, which helps in the early identification and avoidance of potential resonance problems. Maintenance specialists may improve machinery efficiency, reduce operational risks, and increase the lifespan of essential equipment in industrial environments by proactively resolving resonance issues.
Orbit analysis:
Advanced vibration analysis methods like orbit analysis are useful because they plot the circular motion patterns of rotating shafts. Finding important problems such as shaft misalignment, eccentricity, and rotor unbalance is made possible by this study. Engineers can accurately assess possible problems by visualizing and analyzing the orbit patterns, enabling quick corrective action. Maintenance specialists can optimize machinery alignment, increase overall balance, and improve the dependability and performance of rotating machinery in various industrial applications through effective orbit analysis.
Fault diagnosis
Fault Diagnosis is a comprehensive process in vibration analysis, where engineers skillfully integrate multiple techniques to pinpoint specific faults in rotating machinery. One major example is finding the fault through vibration analysis in centrifugal fans. Typical issues addressed through this approach include unbalance, misalignment, bearing defects, resonance, and looseness. Precise fault identification empowers maintenance teams to implement targeted solutions, optimizing equipment performance, reducing downtime, and enhancing the overall reliability of industrial machinery.
Advanced Diagnostic Tools:
Modern vibration analysis is reliant on the use of cutting-edge diagnostic technologies. Engineers need sophisticated software to view, analyze, and interpret vibration data efficiently. The accuracy of defect diagnosis is improved by these cutting-edge tools’ inclusion of features like trend analysis, spectrum overlays, and machine learning algorithms. By utilizing the capabilities of, these technologies, maintenance specialists may develop targeted plans and make decisions to improve the performance and dependability of rotating machinery in many industrial applications.
Advanced vibration analysis is essential to evaluate the health of rotating machinery and guarantee its reliability, safety, and effectiveness in diverse industries. Despite how simple it is to measure vibrations, good data interpretation and root cause analysis require knowledge of case studies and experience.
Vibration analysis is a major approach in condition monitoring services, which is essential for maintaining machine performance. To properly diagnose machine issues, signal extraction must be effective. Techniques for feature extraction are used to identify flaws precisely. Due to the risk of leaks, rotating machinery requires extra safety measures.
Maximise Your Machinery Performance with Technomax
Advanced vibration analysis is a reliable predictive maintenance tool that improves machinery performance across various industries. It helps detect potential issues early, enhance reliability, extend equipment lifespan, and improve workplace safety. These benefits reduce downtime and lower operational costs, allowing for more informed decision-making.
At Technomax, a leading engineering company in UAE, we understand how important it is to keep your machinery running smoothly to improve productivity and minimise costly downtimes. Our advanced vibration analysis and troubleshooting services, as well as other condition monitoring services, are designed to ensure the reliable and efficient operation of your rotating machinery in vivid industrial settings.
Technomax provides expert consultations and proactive maintenance solutions tailored to your industry needs. Our expert team is committed to helping you achieve peak performance, dependability, and equipment longevity.
If you’re looking for ways to improve your machinery performance and operational efficiency, get in touch with us now. We will help you understand how our advanced vibration analysis can support your operations and drive your business forward.
Case Studies On Vibration Analysis
Other Services & Products
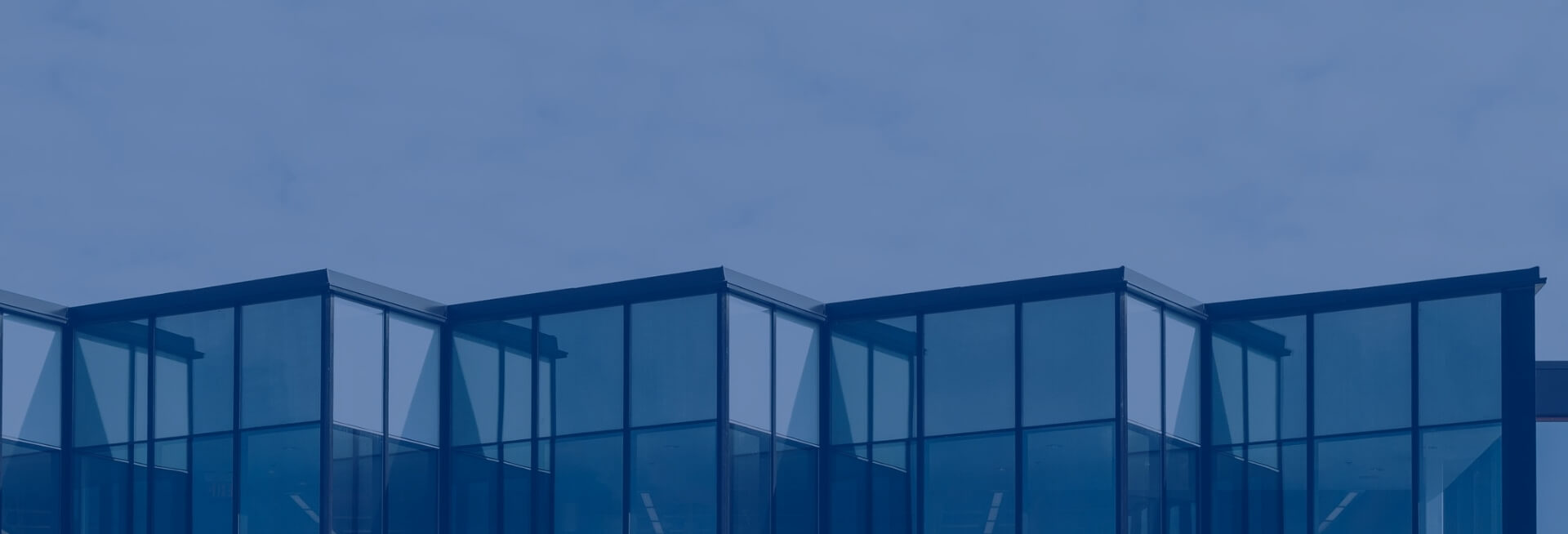
Get Started Now!
It takes less than a minute of your time. Or you may simply call +971 2 555 1 783