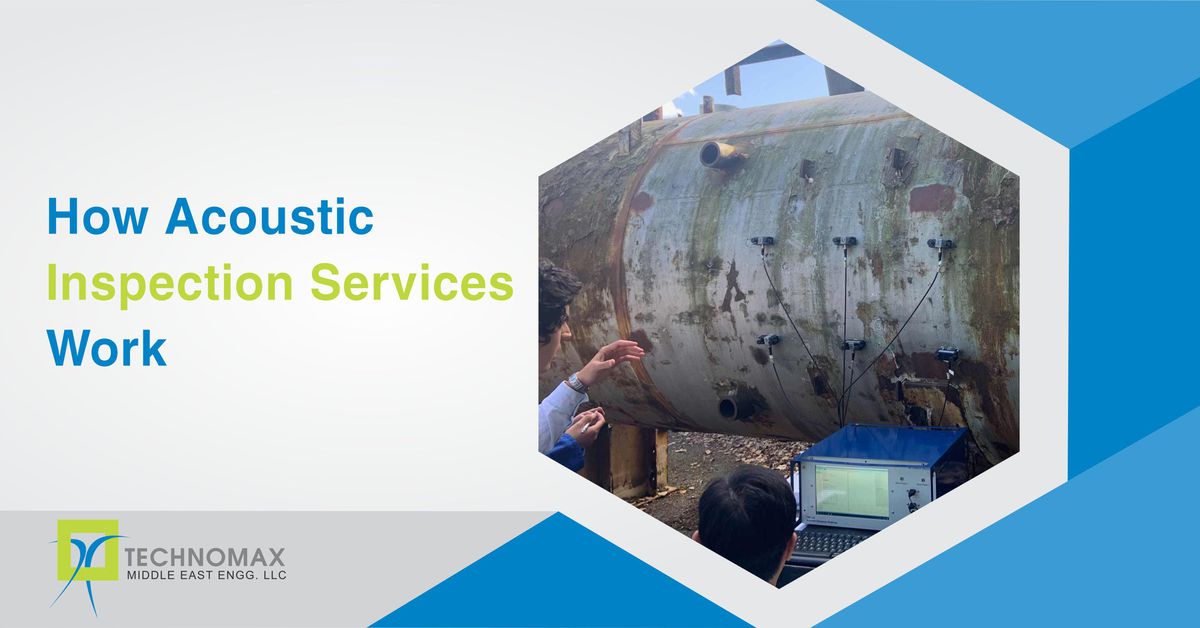
Acoustic Emission Testing (AET) : A Non-Destructive Technique for Detecting Material Defects
What is Acoustic Emission Testing (AET)?
Acoustic emission testing (AET) is a non-destructive testing (NDT) technique that effectively identifies potential issues and flaws before they escalate into more severe problems. These methods can detect potential problems at a very early stage, well before they become an issue, allowing companies to optimize their maintenance and replacement schedules. A type of sound is produced when materials crack, deform, or otherwise become affected. These noises can be very noisy and noticeable at times. They can also be even more subtle, requiring the use of sophisticated equipment to identify.
Acoustic Emission Testing (AET) can detect these quieter sounds, which can expose cracks and other faults forming and may cause significant future problems, such as equipment failure, if not addressed. When a substance deforms under stress, the non-destructive testing (NDT) technique called acoustic emission testing detects and tracks the release of ultrasonic stress waves from localized sources and thus the service is also called ultrasound analysis.
What Causes Acoustic Emissions?
Acoustic emissions occur when a material experiences stress, whether it be from bearing a heavy load or exposure to extreme temperatures. These emissions commonly indicate the presence of a defect or damage within the emitting structure. During an AE test, inspectors focus on identifying such damage.
Potential sources of acoustic emission include:
- Phase transformation
- Thermal stress
- Cracking during cooldown
- Melting
- Failure of bonds and/or fibers
How do Acoustic Emission Testing (AET) Work?
Acoustic inspection services consist of Acoustic emission testing where attaching small sensors to a component that is being tested. The stress waves are translated into electrical signals by the sensors, which are then relayed to an acquisition PC for processing. When the part is subjected to an external stimulus, such as high pressures, loads, or temperatures, the waves are captured. There is a more significant release of energy as the component's damage increases. The rates at which the acoustic emission is detected, called operation, and the strength of the acoustic emission, called loudness, are tracked and used to assess structural integrity and component health.
Acoustic emission can be compared to small earthquakes in the material. Unlike destructive monitoring, this technique continuously tracks a device for faults, allowing large structures and devices to be inspected when in service with minimal disruption. Acoustic emission sources (and thus damage) can be located using multiple sensors. The signal analysis may also be used to assess the existence of various source mechanisms.
The Acoustic Emission Testing (AET) procedure is relatively straightforward. Three transducer sensors are installed on the material's outer surface to detect inconsistencies or flaws by triangulating the emitted acoustic waves.
The specific steps involved are as follows:
-
Attenuation survey: Before conducting the acoustic emission inspection, careful positioning of sensors on the material's surface is crucial for accurate results. Avoiding signal disturbances is essential during sensor placement.
-
Sensor Responses: Assessing the sensor responses allows concluding flaws and defects present in the material.
-
Report: Following the evaluation, AET providers furnish a report to the client, outlining areas of defects and recommending any necessary follow-up non-destructive testing.
Types of Acoustic Emission Testing
Transient Method: The transient method extracts features such as peak amplitude, signal capacity, and burst duration from AE bursts that exceed a threshold (loudness level). These characteristics are then used to determine the state of the item under evaluation. This approach is ideal for inspecting structures for flaws like cracks.
Continuous Method: The continuous method records all AE within a given time frame, such as one-tenth of a second. The average signal level and root-mean-squared (RMS) values are extracted after that. This approach is well suited to applications where there is a lot of background AE or where the AE amplitude is low, such as gearbox testing or leak detection.
Acoustic emission monitoring can be performed in a lab or the field, and it can be done for short periods (a few hours) or more extended periods (a few months). Data can be analyzed remotely using wireless data relay methods.
Also read:
- Crane Inspection: Why and How Often Should We Do It?
- Basics of Vibration Analysis: Sensor Mounting
- Fluid Analysis Testing In UAE
Benefits of Acoustic Emission Testing
Compared to other approaches, acoustic emission has a range of advantages. There are some of them:
- Ability to detect various damage mechanisms in their early stages, such as fiber breakages, friction, collisions, cracking, delamination, and corrosion, until they become significant problems.
- It can be done in the field, during qualification (proof) testing, or during production testing.
- Can locate and distinguish harm sources based on acoustic signatures.
- A structure's global monitoring
- Examines the system or machine in real-operational conditions.
- A non-invasive method
- Extreme temperatures, high pressures, and corrosive and radioactive environments are also potential working conditions.
- Damages in defects that are difficult to reach using traditional nondestructive testing methods may be detected.
Acoustic Emission Testing (AET) at Technomax
Ultrasonic control of equipment, bearings, and moving components uses high-frequency sound waves to detect component faults such as leaks, parts seating, and cavitations. Ultrasonic monitoring is often used as a condition-monitoring tool to detect minor changes in friction forces, which might be overlooked by IR vibration analysis. As a result, UM can be considered an excellent companion research tool along with IR and vibration analysis. UM (ultrasonic monitoring) can aid in almost every aspect of the manufacturing process. It also serves as an early warning system for machine parts rotting, which plant noises and temperatures would otherwise hide.
The techniques include:
- Airborne ultrasonics
- Ultrasonic backscatter technique
- Backwall echo attenuation
- Ultrasonic thickness and gauging, e.g., pipe walls, etc
- Phased array testing
- Automatic and continuous ultrasonic inspection
- Internal rotating inspection systems
- Acoustic emissions testing
- Dry-coupled ultrasonic testing
- Long-range ultrasonic testing
- Acoustic ranging
- Time of flight diffraction
For sophisticated rotating and reciprocating devices, a high level of precision and efficiency is needed since they must operate 24 hours a day, 365 days a year, without even a minor calibration error. Technomax provides condition-based maintenance services to ensure that the systems are in perfect working order. Rather than a calendar-based preventive maintenance program, we use a competitive condition-based predictive maintenance approach. Our condition monitoring services help with proactive maintenance and output planning, which reduces maintenance costs and downtime.
We ensure that you can completely leverage the operating lifespan of the technological components by leveraging our expertise in Condition Monitoring Services and diagnostics.
- It's simple to pinpoint the exact location of a fault.
- Detection of any problems before failure.
- Assist in the development of preventative maintenance techniques.
- Electrical arc flash and leakage inspection
- Detects wear and tear early on.
Technomax's ultrasonic or acoustic inspection services can help you identify early-stage problems in switchgear panels, such as lubrication issues, Steam Trap Inspection, Valve Leak Monitoring, Mechanical Inspections, Air Leak Detection and Quantification, and Partial Discharge Inspection.
FAQs
1. Is there a difference between acoustic emission and ultrasonic testing?
Yes. Acoustic emission testing (AET) and ultrasonic testing (UT) are different methods. AET detects the sound waves emitted by materials under stress, while UT actively sends ultrasonic waves into a material to detect flaws. AET is passive, monitoring real-time structural integrity, whereas UT is an active inspection method.
2. How many types of acoustic emissions are there?
Acoustic emissions can be classified into two main types: continuous emissions and burst emissions. Continuous emissions occur steadily over time, while burst emissions happen as sudden energy releases due to material stress or defects.
3. What is meant by acoustic emission testing?
Acoustic Emission Testing (AET) is a non-destructive testing (NDT) method that detects and analyses stress-induced sound waves within materials. It helps identify defects, cracks, or structural weaknesses by monitoring emitted acoustic signals.
4. What is the acoustic test method?
The acoustic test method involves capturing and analysing sound waves generated by defects in a material. Sensors detect these emissions, and the data is processed to assess structural integrity and identify potential issues.
5. What is the purpose of acoustic testing?
The purpose of acoustic testing is to evaluate material integrity, detect defects, and ensure structural safety. It helps in preventive maintenance, reducing the risk of failure in critical components.
6. What is the difference between acoustic emission testing and ultrasonic testing?
Acoustic Emission Testing (AET) passively listens for sound waves emitted by materials under stress, while Ultrasonic Testing (UT) actively sends high-frequency sound waves into a material to detect flaws. AET is ideal for continuous monitoring, whereas UT is used for precise flaw detection at specific locations.
Learn More About Our Services
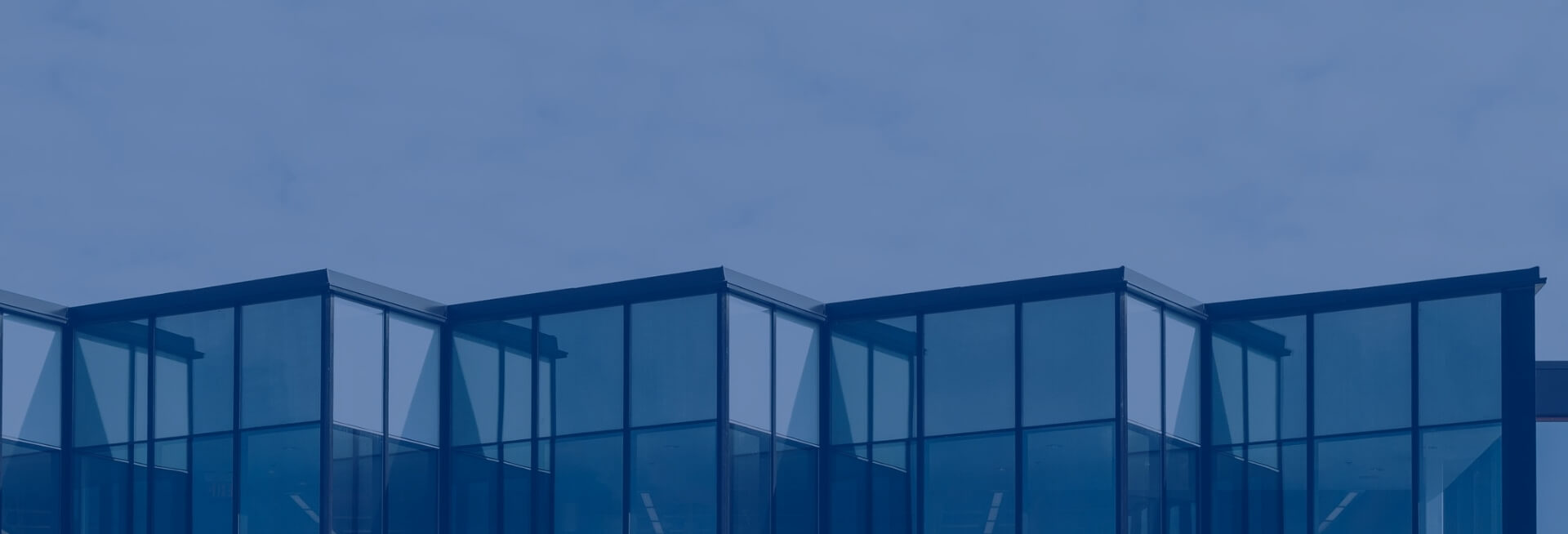
Get Started Now!
It takes less than a minute of your time. Or you may simply call +971 2 555 1 783