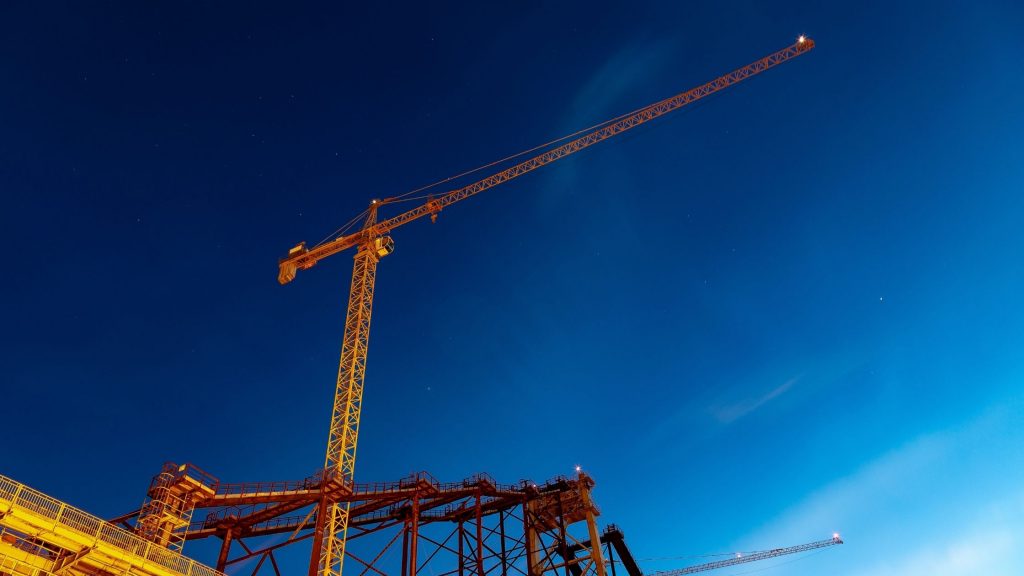
A counterweight functions as the stabilizing component within a balancing system for lifting mechanisms or machines. It finds application in various equipment such as lift trucks, drawbridges, elevators, cranes, and any machinery designed for heavy lifting.
How Do the Counterweights in Tower Cranes Work? Did you ever think about this question? We mostly take for granted how these massive devices form our surroundings. It's difficult to understand how the crane does what it does without falling over from a distance or the deck. It's difficult to imagine how anything so significant might be built without anything equally large next to it to aid in the process. Cranes combine sheer height with the ability to carry heavy materials easily up to several floors. Without cranes, this job becomes challenging and time-consuming, so cranes help speed up the building process while still making it much simpler. If you are looking for crane installation in Abu Dhabi, this guide will give you an insight into how counterweights work on tower cranes.
Also Read:
- Common Uses Of The 1 Ton Overhead Crane
- How To Calculate The Capacity Of The Crane Compared To Depth | Crane Capacity
- How Do Cranes Get Erected On Construction Site – Crane Erection
- Standard Crane Hand Signals for Crane Operations Safety
How is a Tower Crane Installation Done?
Before a tower crane can be assembled, foundations must be dug for it, and the crane's bottom portion must be fixed to steel rods in the foundations. After the concrete has hardened, the crane can be assembled section by section. The tower crane parts are held in place by a mobile crane, which is fixed with a hydraulic wrench. The turntable, where the cabin sits, is the heaviest component of the crane, and once it is in place, the articulated arm, also known as the jib, can be wrenched on.
Ropes and a trolley system are added to the jib for the tower crane to work, and it is wired up to the control pad in the cabin. To offset the weight that the crane will be raising, a counterweight is attached to the opposite end of the articulated jib. Many cranes have an adjustable counterweight depending on how much weight is being raised, but the weight is usually secured just short of the jib's end. The crane may also be braced to the side of buildings to hold it upright, although this is only possible if the building being operated on is already at a significant height.
Types of Cranes and Corresponding Counterweight Systems
Counterweights play a crucial role in maintaining balance and stability during the lifting process for various types of cranes, including mobile ones like crawler cranes, truck cranes, and terrain cranes. Operators can add or remove these counterweights at the rear of the crane to accommodate different lifting capacities.
- Mobile cranes may employ a combination of fixed and adjustable counterweights to achieve the necessary balance for specific lifts.
- Tower cranes, commonly found at construction sites, feature a vertical mast, a horizontal jib, and a counter-jib that supports the counterweights. At the opposite end of the jib, the counterweights uphold the crane's equilibrium and stability during lifting operations. Operators can make adjustments to the number and size of counterweights based on the load weight and jib reach, ensuring optimal performance and safety.
Let's go through a detailed analysis of Counterweights in the Tower Crane
What are the Counterweights in the Tower Crane?
Counterweights must have the right mass and be at the right distance from the pivot point to function as effectively as possible. This is known as the moment of physics, and it is the counterweight's mass multiplied by its distance from the pivot. When lifting or lowering loads, counterweights provide additional support. The counterweight moment must be equal to the moment of the load for the most effective operation. This is critical because if one side's moment is greater than the other's, the dominant side will tip over.
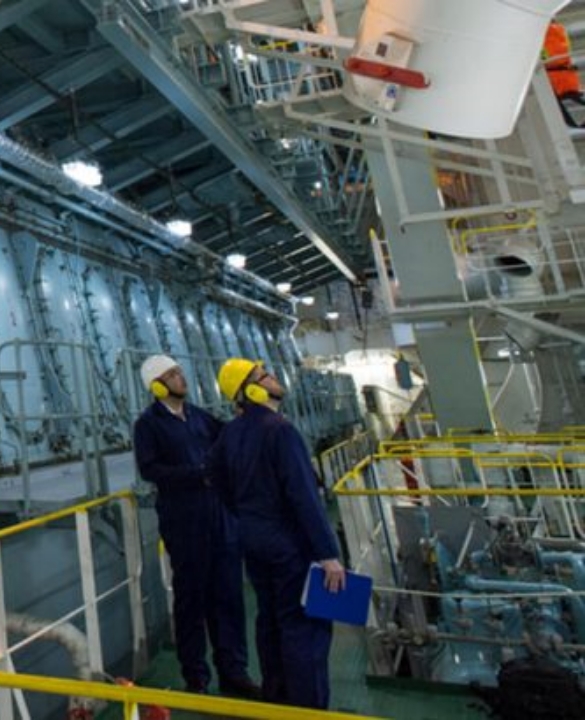
What is the Purpose of a Counterweight in Tower Crane Installation?
When it comes to cranes, counterweights are also crucial for job protection in the construction zone. A crane counterweight aims to keep the crane from tipping over. The counterweight is used to balance the weight of the object being lifted. Most of the time, these weights support cranes to hoist heavy loads or dig into the ground. Although counterweights do not move very quickly, it is essential to be cautious when working with them. If you're walking by the counterweight, make sure the crane operator knows you are there, so you don't get stuck between the counterweight and any stationary objects nearby. Between the two points, you might be pinched and seriously wounded, if not killed. The counterweight is crucially significant. If it isn't built correctly and isn't the right size and shape, it becomes a complicated topic that can cause the vehicle to tip over in the load's direction or backward. If the counterweight setup is too light for the load and booms the configuration, a crane will fall over in the load's direction while attempting to lift it. Otherwise, a crane's counterweight will tip it backward in the following situations:
- For the boom setup, the counterweight is too high.
- The crane is traveling up a slope.
- Insufficient timbers are mounted under the outrigger pads below the counterweight while the crane is on soft land.
- Outriggers or any other ground support cannot withstand the combined weights and tipping forces because they are not extended or lowered into place.
- If the boom configuration is raised too high and not enough weight is added to it
Calculating the Correct Counterweight Helps Avoid Mishaps at the Crane Site
The most common cause of toppling is a mathematical error. As a result, it is critical to determine the correct weight and size before the manufacturing process during the design phase. This is the only way to ensure the crane counterweight's safe operation. When designing the part, use the following mathematical formula to reduce potential risks and provide an efficient counterbalance:
P =V x μ x g
P is the requisite counterweight's weight; V is its volume; –μ is the density of the material used to make the counterweight, and g is the gravitational constant (9.81).
Why do Manufacturers Prefer Iron Counterweights?
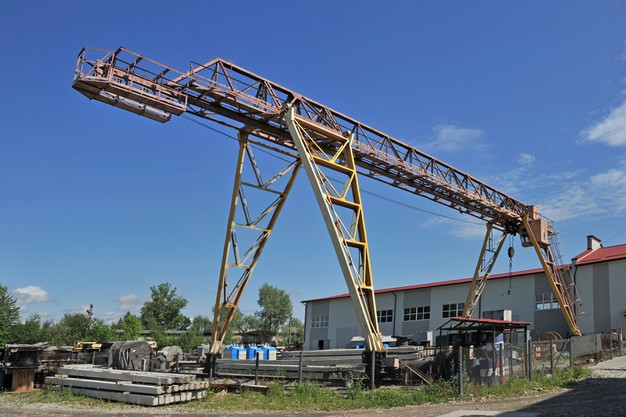
Complete cast iron, full concrete, or a combination of concrete and metal bits are preferred by the manufacturers. Metal forklift counterweights, for example, are widely used to maximize space efficiency. However, some industries, such as agriculture (tractors) and off-highway (excavators and cranes), have counterweight requirements that both metal and concrete can meet. While concrete is less expensive than iron, it is preferable because concrete applications are vulnerable to many issues that cast iron counterweights can solve. The advantages of using iron counterweights include-
- Dense aggregates such as limonite, hematite, or magnetite and metal bits and fragments can be used to increase the density of concrete. This raises the cost of concrete significantly, but it also has a lower density than iron.
- Concrete becomes more costly to cut out the desired form in applications where counterweights must fit into unique shapes, such as tractor suitcase counterweights, which are formed differently depending on the space on the rear axle of tractors. When shaping cast iron into a smoother form, cracking is less likely to occur.
- Since cast iron is denser than other materials, cast metal counterweights have a density of three times that of pure concrete. Compared to concrete, this allows iron to reach the target weight in less space and volume, reducing the expense of supplementary material.
- Cast iron, unlike concrete, is a recycled commodity that does not necessitate the extraction of fresh raw materials.
Conclusion
Crane counterweights hold the vehicle steady and upright, ensuring secure service. For the performance of a high-quality counterweight, best construction practices, the most durable raw material range, such as grey cast iron, and frequent safety inspections are needed.