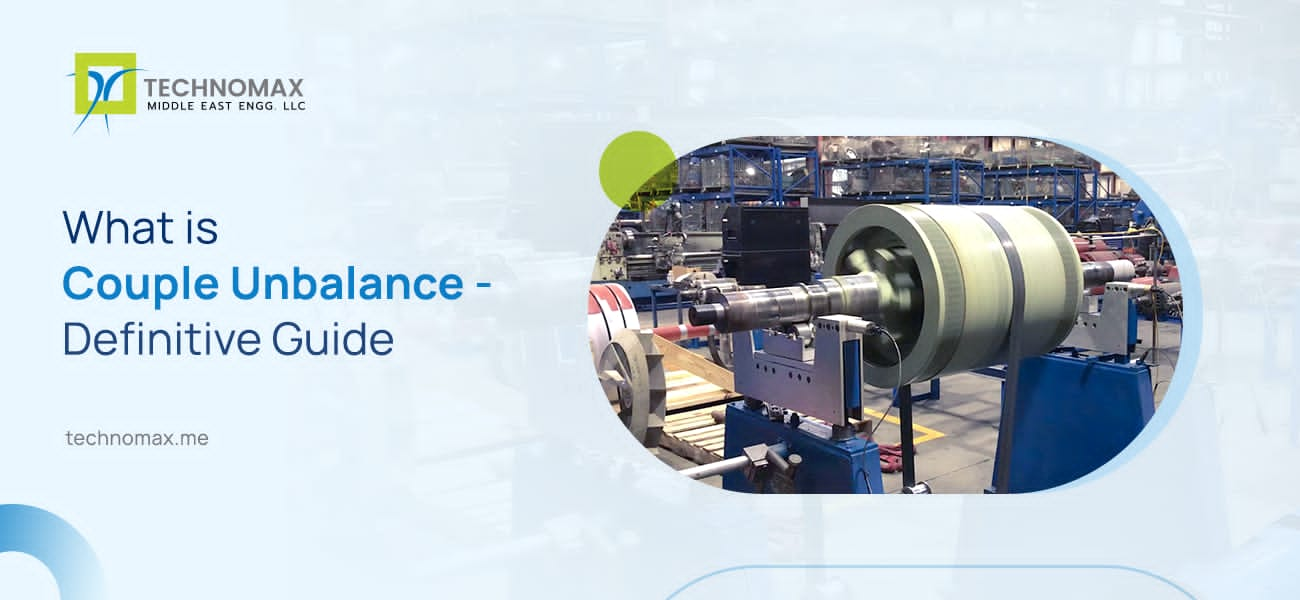
Rotor enables the conversion of electric and electromagnetic energy to rotational motion. The reliable operation of the rotors depends upon the equal weight distribution along the rotational axis. Leaving one side with too much weight can cause an uneven mass distribution termed as “unbalance”.
This is a product of uneven mass distribution, which results in the vibration of the machine. The rotation-causing interaction of unbalanced mass components with the radial acceleration develops a centrifugal force, which causes the rotor to move through the line of action of the force.
In this blog, let’s delve deeper into the concept of couple unbalance, its effects, the need for couple balancing, and the correcting techniques.
You may also like to read:
- Preventive Maintenance Using Vibration Analysis in Electric Induction Motors
- Types of Misalignment in Machines
- Rotodynamic Analysis Services from Technomax
Couple Unbalance– Definition
Couple unbalance, otherwise known as the moment unbalance, refers to the state where the two equally sized unbalances have the angular positions set 180° from each other. You can’t use knife edges to detect this unbalanced distribution like the static unbalance technique since the rotor does not maintain a unique position while at rest.
Since the two unbalanced exert a moment, the rotor implements a wobbling motion along the axis perpendicular to the rotating axis — i.e., the vertical axis. Hence, this form of unbalanced distribution is known as the couple unbalance.
Usually, the couple unbalance arises when every bearing plane is not exactly perpendicular to the axis of rotation. Once the rotor spins, it produces vibrations with twisting movements. A couple unbalance needs two corrections instead of correcting them in one plane.
Importance of Understanding Couple Unbalance
The force that unbalance creates can destroy the life of the machine— this could be detrimental to the bearings, rotors, and supporting structure. The amount of force unbalance creates is based on the rotational speed and the extent of unbalance.
Unbalance causes deterioration to the safety and the operational functioning of the machinery, which impacts the working of the rotor. With rotor balancing, you can eliminate the issues that unbalance causes, thereby minimising the noise and vibration to improve the life of the system.
Overview of Rotational Dynamics
Rotational Motion– An Overview
Rotational motion means the motion of an object along a circular direction, across a fixed orbit. The rotational motion dynamics are analogous to both translational and linear dynamics.
The motion equation of linear motion and the equations for rotating equipment mechanics work similar to each other.
Considering the rotational motion, you need to check only the rigid bodies which have a mass and hold a rigid shape.
Dynamics of Rotational Motion
- Moment of Inertia: It measures the resistance of the object in changing the rotation. The moment of inertia is expressed as ‘I’ and measured in kg/m2. The moment of inertia I= mr2, where m denotes the mass of the particle, and r denotes the distance calculated from the axis of rotation. The larger the mass, the higher the moment of inertia.
- Torque: Torque refers to the twisting effect of the force being applied to the rotating equipment, placed at position ‘r’, away from the rotating axis.
- Angular Momentum: Angular Momentum or L measures the difficulty of shifting a rotating object to the rest position.
Consequences of Couple Unbalance
Unbalance can create many negative effects on both the surroundings and the rotating equipment. The most significant effect is vibration caused due to the centrifugal force of the unbalanced mass.
This oscillation of the rotor around the axis can damage the shaft, bearings, couplings, seals, and other elements of the machine, transmitting it to the structure, foundation, and piping. Vibration also creates noise, which affects the equipment and the workers.
The other effects of unbalance include heat, which is produced due to the deformation, and friction due to the vibration of the machine. Heat can minimise the lubrication, performance, and lifespan of the equipment, while also increasing the risk of explosion or fire.
Detection & Measurement of Couple Unbalance
Early detection and prevention of the couple unbalance helps the machine to improve durability. Since the equipment can last longer, it increases the productivity and reliability of the machine. Early detection also helps to lower the dresses that might deteriorate the life of the bearings.
Methods of Detecting and Measuring Couple Unbalance
- Vibration Analysis: The vibration analysis technique tracks the vibration levels and patterns within an equipment, structure, or machine. This detects the abnormalities in the vibration processes and helps to evaluate the entire condition of the test object.
- Balancing Techniques: You can use various balancing techniques to detect the couple balance— spinning the object, considering a frame to let the object vibrate perpendicularly across the axis of rotation, and detecting unbalance through sensing vibration displacement, velocity, and instantaneous acceleration.
- Condition Monitoring: This maintenance approach assesses the machine's health and safety with the machine sensor data and other real-time parameters taken together. This technique helps the plant maintenance technicians track the health of each system and gives a comprehensive view of the mechanical processes.
Correcting Couple Unbalance
Static Balancing
Static balancing occurs while the centre of gravity for a specific object lies on the axis of rotation. This lets the object stay stationary while having the axis horizontal with no braking force applied. It doesn’t exhibit the tendency to rotate with the force of gravity.
Dynamic Balancing
Dynamic balancing is where the rotation causes no centrifugal force, but only needs the force to support its weight. While a system is unbalanced for eliminating the stress that affects the bearings, adding a counterbalancing weight is encouraged.
Balancing procedures and techniques
After locating the heavy spot, adding mass to the rotor on the opposite end as additional weight or eliminating weight from a heavy location can help to correct unbalance. Drilling, milling, and grinding can help to remove the weight from the rotor while bolting and welding weights can help to add weight to the rotor.
Role of Technomax in Couple Balancing Services
Balancing the machinery regardless of being static or dynamic, is the core factor behind the elimination of frequent performance concerns. These concerns include noise, vibration, and heat. Avoiding these will help to extend the lifespan, scale accuracy, and eradicate premature system failures.
With skilled experts and a reliable dynamic balancing service provider, you can encourage the balancing of equipment with high accuracy. At Technomax, our team of experts provides you with the best forms of balancing to ensure your machine functions as efficiently as possible.
With decades of experience, we offer balancing of multiple ranges of rotating equipment like rotors, shafts, impellers, turbines, and many more. To know more about the couple balancing services we provide, let’s get in touch.
Learn More About Our Services
Recent Blogs
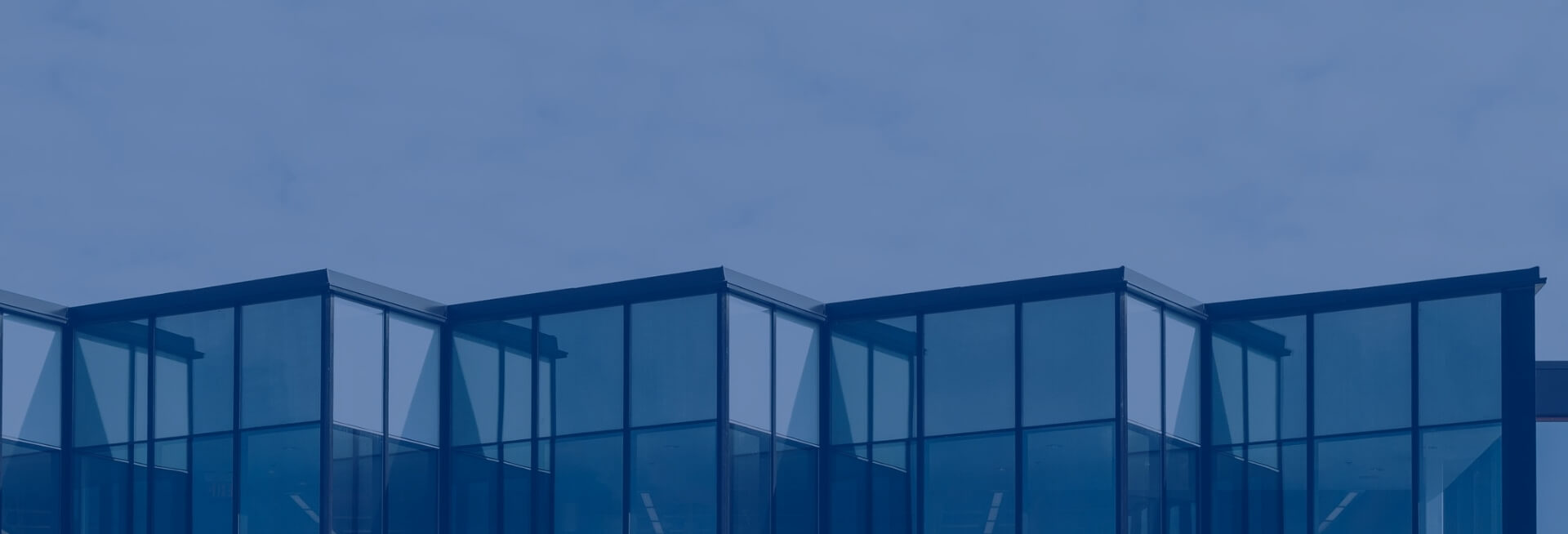
Get Started Now!
It takes less than a minute of your time. Or you may simply call +971 2 555 1 783