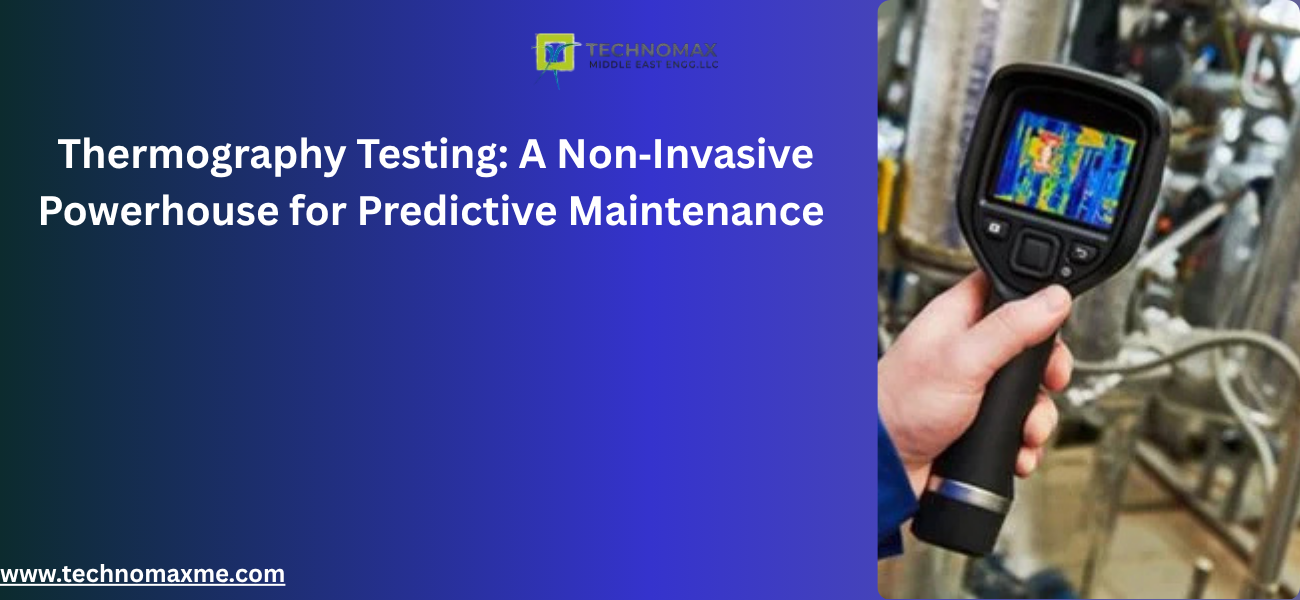
Thermography Testing: A Non‑Invasive Powerhouse for Predictive Maintenance in Modern Industry
Thermography testing involves the use of infrared technology to detect and map temperature variations across equipment and operational areas. It helps monitor heat distribution and compare temperatures among different components. Infrared thermography makes it possible to visualise these heat patterns as thermal energy cannot be seen with our naked eyes. This temperature analysis enables early detection of issues. This effective method of predictive maintenance helps to find equipment failure or unplanned downtime.
Industrial facilities today are under intense pressure to maintain uptime, cut operational costs, and meet safety and sustainability targets. Equipment failures can halt production, jeopardise employee safety, and erode customer confidence in a single unplanned shutdown. Thermography testing has emerged as one of the most versatile, cost‑effective, and non‑invasive diagnostic techniques against this backdrop.
Thermography testing encompasses a range of methods for visualising heat. By detecting, recording, and analysing temperature differences on the surface of electrical or mechanical assets, thermography makes the invisible visible. This predictive maintenance reveals developing faults long before they become critical.
Lets analyse more details on thermography testing, how it works, the different approaches available.
What Is Thermography Testing?
Thermography testing helps to detect and map the heat signature of an object or area using a specialised imaging system like a thermal or infrared camera. Every object above absolute zero (-273.15 °C) emits infrared radiation and a thermography device can translate those emissions into a colour‑coded “thermogram” that displays even minute temperature differences.
This thermogram plays an important role in predictive maintenance by helping identify potential issues that may cause equipment failure and unexpected shutdowns. The strength of this technique is its ability to detect anomalies in real time while the system remains under load. If there is a hot fuse or an overheating motor bearing, thermography testing will allow you to avoid major breakdowns and carry out scheduled repairs.
There are different types of thermography testing for predictive maintenance depending on the asset. Let's have a look into it.
Types of Thermography Testing
Thermography testing can be classified into several types based on the method of heat detection and the application area. Each type serves specific industrial needs and helps ensure accurate, non-contact inspection of equipment and structures. Understanding the differences helps you choose the right method for each asset or problem:
Type | Overview | Ideal Use Cases |
Infrared Thermography | Passive, sees natural heat emissions; typically hand‑held or drone‑mounted cameras | Electrical panels, motors, bearings, building envelopes |
Active Thermography | Adds external energy (heat, electrical load, or flash) to provoke a stronger response | Composite material inspection, micro‑crack detection, aerospace components |
Passive Thermography | Observes an object naturally cycling through temperature changes, such as day/night shifts | Large solar farms, building façade studies |
Ultrasonic‑Assisted Thermography | Couples ultrasound waves with thermal imaging to highlight subsurface defects | Bonded structures, multilayer laminates, pipeline corrosion |
For most industrial facilities, infrared thermography testing remains the workhorse as it is simple to deploy yet incredibly revealing. If you need a specialised approach, Technomax can advise on and execute the appropriate methodology.
Thermography Testing Procedure: Five Practical Steps
- Asset Criticality Ranking – List equipment by failure risk and downtime cost to target high‑value assets first.
- Baseline Survey – Conduct an initial “reference” scan to capture normal operating temperatures.
- Periodic Re‑scans – Schedule quarterly or semi‑annual follow‑ups; frequency depends on asset criticality and operating environment.
- Data Management – Store thermograms in a CMMS or cloud platform to enable trend analysis.
- Corrective Actions & Verification – Repair identified issues, then re‑scan to validate that the anomaly has cleared.
Following this cycle converts raw infrared data into tangible operational gains.
Role of Infrared Cameras in Effective Thermography Testing
In the field of thermography testing, the accuracy and reliability of results heavily depend on the quality of the infrared camera used. Infrared Cameras Inc. (ICI), a leading manufacturer of infrared imaging systems, offers a comprehensive range of thermal cameras that are widely used across industrial applications. At Technomax, we supply and support ICI infrared cameras to empower professionals with cutting-edge thermal imaging technology for precise diagnostics.
ICI infrared cameras are engineered with advanced sensors capable of detecting even the slightest temperature variations. This feature makes them ideal for predictive maintenance, electrical fault detection, and mechanical equipment analysis. Their high-resolution imaging and real-time temperature tracking allow users to visualize invisible heat signatures, identify anomalies, and take corrective action before equipment failure occurs. Whether it’s monitoring switchgear, transformers, motors, or insulation systems, these cameras provide dependable performance even in demanding environments.
Key Features of ICI Infrared Cameras
- High-Resolution Thermal Imaging—Captures clear, detailed thermograms for easy fault detection.
- Wide Temperature Range—Monitors extreme temperature conditions with high accuracy.
- Software Integration—Includes reporting, data logging, and remote access capabilities.
- User-Friendly Interface—Intuitive controls and real-time display for fast inspections.
- Customizable Options—Available in handheld, portable, and fixed-mount models.
- Compatible with Various Industries—Designed to meet the needs of power plants, oil & gas, manufacturing, and more.
Advantages of ICI Infrared Cameras in Thermography Testing
Infrared cameras play a vital role in the accuracy and reliability of thermography testing by capturing detailed thermal images that reveal temperature variations across equipment and systems.
- High Sensitivity and Accuracy – Detects even the smallest temperature differences for precise diagnostics.
- Non-Contact and Real-Time Monitoring – Enables safe, uninterrupted inspections of live equipment.
- Versatile Applications – Suitable for electrical systems, mechanical components, HVAC, and building diagnostics.
- Enhanced Predictive Maintenance – Identifies faults early to prevent costly breakdowns and downtime.
- Reliable Performance in Harsh Conditions – Built for industrial environments with rugged design options.
- Improved Safety – Helps detect fire hazards, overheating, or insulation failures without physical contact.
- Data-Driven Insights – Supports maintenance planning with accurate thermal data and trend analysis.
Real‑World Industrial Applications of Thermography Testing
- Electrical Distribution Systems — Locate loose connections, phase imbalance, overloaded breakers, or failing transformer windings before they trigger arcing or fires.
- Rotating Machinery — Identify bearing wear, misalignment, or inadequate lubrication by spotting abnormal heat around bearing housings and shafts.
- Process Heaters and Boilers — Detect refractory insulation damage, burner malfunctions, or heat exchanger fouling without opening the unit.
- HVAC & Building Diagnostics — Pinpoint air leaks, insulation voids, and moisture intrusion to improve energy efficiency.
- Renewable‑Energy Assets — Map hot cells in PV panels or overheated cabling in wind‑turbine nacelles, preventing drastic output losses.
- Oil & Gas Facilities — From flare‑stack monitoring to pipeline corrosion assessment, thermography keeps critical infrastructure running safely.
By integrating thermography into a larger condition‑monitoring services, companies extend asset life, reduce downtime, and bolster safety compliance.
Applications of Thermography Testing in Industrial Maintenance
Thermography testing plays a critical role in industrial maintenance by providing non-contact, real-time thermal analysis of equipment and systems. It enables maintenance teams to detect early signs of wear, overheating, and failure without disrupting operations. In manufacturing environments, thermography supports a wide range of preventive and predictive maintenance activities. Below are some of the most common and impactful applications:
1. Bearing Temperature Monitoring
Bearings are essential components in rotating equipment, and their failure can result in severe damage and unplanned downtime. One of the earliest signs of bearing problems is abnormal heat generation. Friction due to insufficient lubrication can cause temperatures to rise as metal components make direct contact. Interestingly, even over-lubrication can increase temperatures, as the lubricant shears under movement and generates excess heat.
Thermographic testing allows maintenance personnel to identify these temperature anomalies early. By detecting potential bearing issues before they escalate, companies can prevent costly breakdowns and extend the lifespan of machinery.
2. Electrical Panel and Insulation Inspection
Electrical cabinets and control panels are another key area where thermography proves invaluable. Over time, components such as breakers, fuses, and connectors may degrade, increasing electrical resistance and generating excess heat. If left unchecked, these conditions can lead to component failure, safety risks, and unplanned outages.
Infrared thermography offers a fast, accurate method to scan and monitor electrical systems without powering them down. It also helps detect insulation breakdown by highlighting areas where heat is escaping, allowing for proactive replacement of deteriorating materials. This ensures safety, energy efficiency, and uninterrupted operations.
3. Leak Detection in Pressurised Systems
Leaks in pressurized equipment often lead to localized temperature changes. Thermographic imaging can detect these subtle variations, providing a visual indicator of leak points. This allows maintenance teams to quickly identify and address issues before they escalate into major failures or system shutdowns.
Detecting leaks early also contributes to energy savings, improves equipment reliability, and supports compliance with environmental and safety standards.
4. Process Temperature Monitoring and Analysis
In process industries, maintaining consistent operating temperatures is crucial for product quality and system stability. Thermographic testing can be used to monitor temperature distribution across process equipment, such as heat exchangers, reactors, ovens, and pipelines.
By comparing real-time thermal data against defined thresholds or historical benchmarks, technicians can identify abnormal conditions such as overheating, underperformance, or thermal imbalance. This enables prompt corrective action and improves the overall efficiency of the process.
Why Choose Technomax for Thermography Testing?
Thermography testing simultaneously boosts uptime, slashes maintenance budgets, and safeguards personnel without touching, halting, or damaging the asset being inspected. Whether you manage a single facility or a geographically dispersed portfolio, integrating thermography into your maintenance toolkit is one of the smartest, quickest ways to drive reliability.
Being the leading experts of Thermography Testing in UAE and Middle east, Technomax integrates it with complementary techniques such as vibration analysis, partial‑discharge testing, and oil analysis to give you a 360‑degree view of asset health.
Ready to convert hidden hot spots into actionable insight? Talk to Technomax’s Infrared Thermography Specialists and discover how a tailored inspection plan can fortify your plant against unforeseen failures.
Frequently Asked Questions
- What is thermography testing used for?
Thermography testing is used to detect heat variations in equipment, structures, and systems.
It helps identify electrical faults, mechanical wear, insulation defects, moisture intrusion, and more.
By flagging issues early, it enables proactive maintenance and reduces costly downtime. - What is the purpose of a thermograph?
A thermograph captures and records temperature patterns across a surface in real time.
It produces visual thermograms that highlight abnormal heat signatures invisible to the naked eye.
These images allow engineers to diagnose faults and prioritise corrective actions. - What is the principle of thermography testing?
Thermography is based on the principle that all objects emit infrared radiation proportional to temperature.
Thermal cameras detect this radiation and convert it into a colour‑coded image or numerical data.
Temperature anomalies appearing on the thermogram guide inspectors to potential problem areas. - What conditions can thermography detect?
Thermography can uncover overheating electrical connections, bearing failures, misalignment, and friction in machinery.
It also reveals insulation breakdown, moisture ingress in building materials, and HVAC inefficiencies.
These insights facilitate early interventions, enhancing safety and extending asset life.
Learn More About Our Services
Recent Blogs
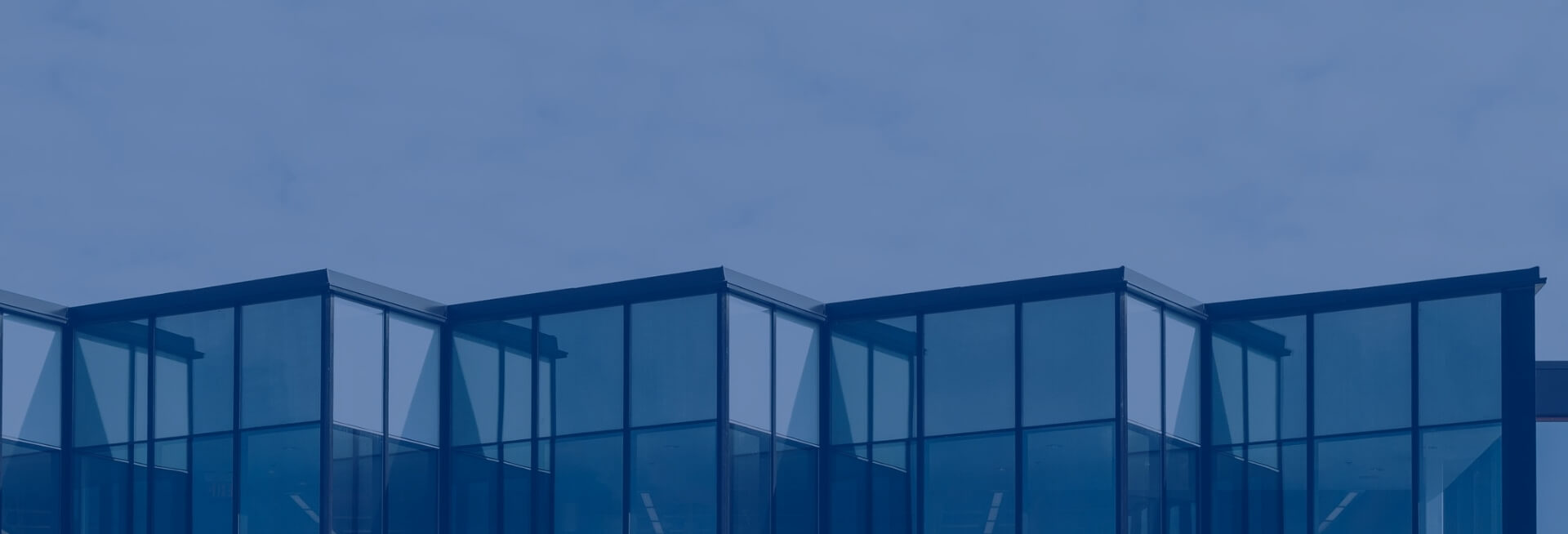
Get Started Now!
It takes less than a minute of your time. Or you may simply call +971 2 555 1 783