- Services
- In-Situ Dynamic Balancing
In-Situ Dynamic Balancing
In-Situ Dynamic balancing is a crucial process for maintaining the performance, reliability, and safety of rotating machinery. By addressing imbalances and minimizing vibrations, this service optimizes equipment efficiency, prolongs its operational life, and reduces the risk of damage and downtime. Through a systematic approach involving assessment, measurement, correction, verification, and documentation, rotor balancing ensures that machinery operates smoothly and efficiently in its intended environment. It is a specialized technique that involves balancing rotating machinery while it is running in its original environment, instead of dismantling and transporting it to a different balancing facility. This service is critical in maintaining the performance, dependability, and safety of various types of equipment, such as industrial fans, pumps, turbines, motors, and other rotating machinery.
Dynamic balancing aims to reduce vibrations that arise from imbalances in rotating components. A machine that is not balanced can lead to several negative effects, including increased wear and tear on components, reduced equipment lifespan, decreased efficiency, and potential safety hazards. I you are looking for In-situ dynamic balancing in UAE & Middle East, then Technomax helps identify and correct these imbalances to optimize the machinery’s performance and prolong its operational life.
Benefits of In-Situ Dynamic Balancing
- In-situ dynamic balancing can be performed without dismantling the machinery
- This minimizes downtime and eliminates the logistical challenges associated with transporting large and complex equipment to an external balancing facility.
- In-situ balancing allows for more precise balancing results, as the machinery is tested under actual operating conditions based on the factors such as temperature, load variations, and environmental influences.
What is In-Situ Dynamic Balancing?
The process of in-situ dynamic balancing involves several crucial steps. Firstly, a team of trained professionals visits the site where the equipment is installed. They conduct a thorough assessment of the machinery, examining its condition and identifying the vibration analysis any signs of imbalance or vibration-related problems. This initial assessment helps determine the extent of the balancing process and the specific areas that require attention.
The next step is measurement and analysis. The professionals use specialized equipment, such as vibration analyzers or portable balancing devices, to measure the vibrations produced by the machinery. These measurements provide valuable data on the amplitude, frequency, and phase of the vibrations, allowing the professionals to identify the exact locations and severity of the imbalances.
How We Perform It?
Once the measurements are obtained, the professionals proceed with the correction phase. Based on the measurement data, they determine the appropriate corrective actions needed to balance the machinery. This can involve adding or removing weight from specific locations on the rotating components. Balancing weights may be added using methods such as weld-on weights, adhesive weights, or clamp-on weights. The professionals may also use specialized adjustment techniques to correct imbalances, such as shifting the position of a component or modifying its shape.
After the corrective actions are implemented, the professionals re-measure the vibrations to ensure that the imbalances have been adequately addressed. This verification step is essential to confirm the effectiveness of the balancing process. If the vibrations are still not within acceptable limits, further adjustments may be made until the desired balance is achieved.
Throughout the process of in-situ rotor dynamic balancing, the experts maintain thorough records of the entire procedure. They record the initial measurements, describe the corrective actions taken, document the final measurements, and suggest any recommendations for ongoing maintenance or monitoring. This documentation serves as a valuable resource for future inspections and helps track the history of the machinery’s balancing efforts.
In-situ Dynamic Balancing from Technomax
It is crucial to note that in-situ dynamic balancing requires expertise in vibration analysis and balancing techniques. Trained professionals with knowledge and experience in this field are best suited to perform these services. All the condition monitoring services can be done with precise calculations and timely manner. At Technomax, we possess the necessary skills and equipment to carry out the assessment, analysis, correction, and verification steps effectively. Ensure the safety of your machines with us.
Other Services & Products
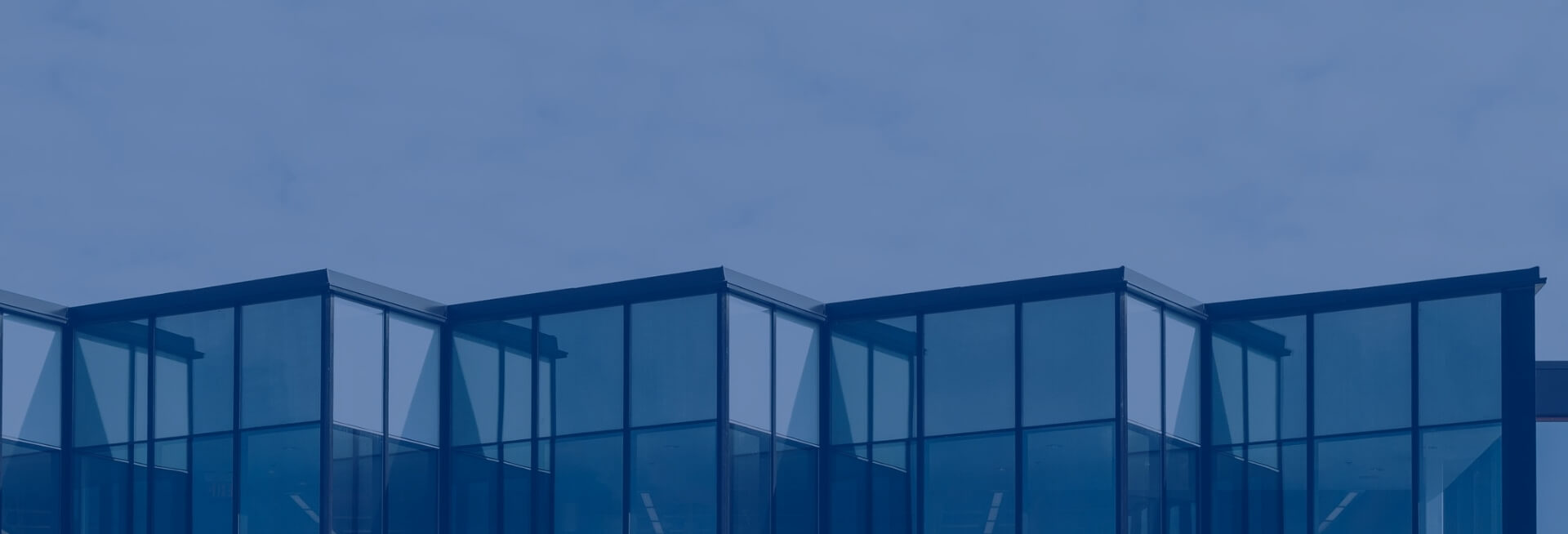
Get Started Now!
It takes less than a minute of your time. Or you may simply call +971 2 555 1 783