- Services
- Structural Vibration Analysis
Structural Vibration Analysis
Structural Vibration Analysis is a powerful tool that allows engineers to study how a structure responds to vibrations. This proactive approach aids in averting resonance issues, thereby ensuring the safety and stability of the structures.
Vibration is a common phenomenon experienced by various structures, rotating machines, turbines, buildings, and bridges. Understanding and effectively managing vibration is essential for industries to ensure optimal performance and prevent potential failures.
Importance of Vibration Structural Analysis
Just like humans, machines are also subject to vibration, caused by factors like instability in rotating machinery, ground vibrations, and neighboring machines’ vibrations. Hence, it is crucial for industrialists to comprehend vibration and implement effective solutions to control and minimize its impact. Structural Vibration Analysis plays a vital role in addressing vibration-related challenges, ensuring smooth operation, and reducing maintenance costs.
Addressing Vibration-Related Breakdowns
Dynamic loads, such as unbalance, misalignment, pulsation forces, and others, can lead to localized structural resonance in machines. Structural resonance often becomes a significant source of vibration-related breakdowns in various facilities, affecting piping and mechanical systems. To prevent such failures, vibration engineering service providers, like Technomax, come into play.
Technomax in Vibration Structural Analysis
- Proper understanding of Dynamic Forces: Technomax conducts comprehensive pulsation breakdown, mechanical computation, and engineering studies to determine dynamic forces generated by machinery (frequency, amplitude, changes by operating condition, etc.).
- Dynamic FE Model Adjustments: The dynamic FE model is refined through field testing, dynamic vibration studies, and additional field calculations. Technomax applies field outcomes to dynamic FE models to get valid findings.
- Correct Boundary Conditions: Technomax ensures the correctness of borderline condition assumptions, as the flexibility of the support structure can significantly influence the dynamic behavior of identical units on a platform.
- Efficient Analysis with Advanced Technology: Technomax employs cutting-edge software and technology to recast structural models into dynamic models, enabling more systematic analysis.
Benefits of Technomax's Approach
Technomax’s simplified procedure of Structural Vibration Analysis reduces overall maintenance costs and improves reliability for equipment and structures. Their integrated solution, deploy on collective field experiences, ensures uninterrupted operations, eliminating long-term vibration problems and managing integrity vulnerabilities.
Wrapping Up
Structural Vibration Analysis is a crucial aspect of ensuring the stability and efficiency of engineering structures. Technomax’s expertise in vibration engineering and integrated approach provides reliable solutions to tackle vibration-related challenges, reducing equipment failures, and improving reliability. By deploying condition-based predictive maintenance techniques and offering proactive approaches, Technomax’s monitoring solutions enable industries to achieve enhanced performance and better equipment diagnostics.
Other Services & Products
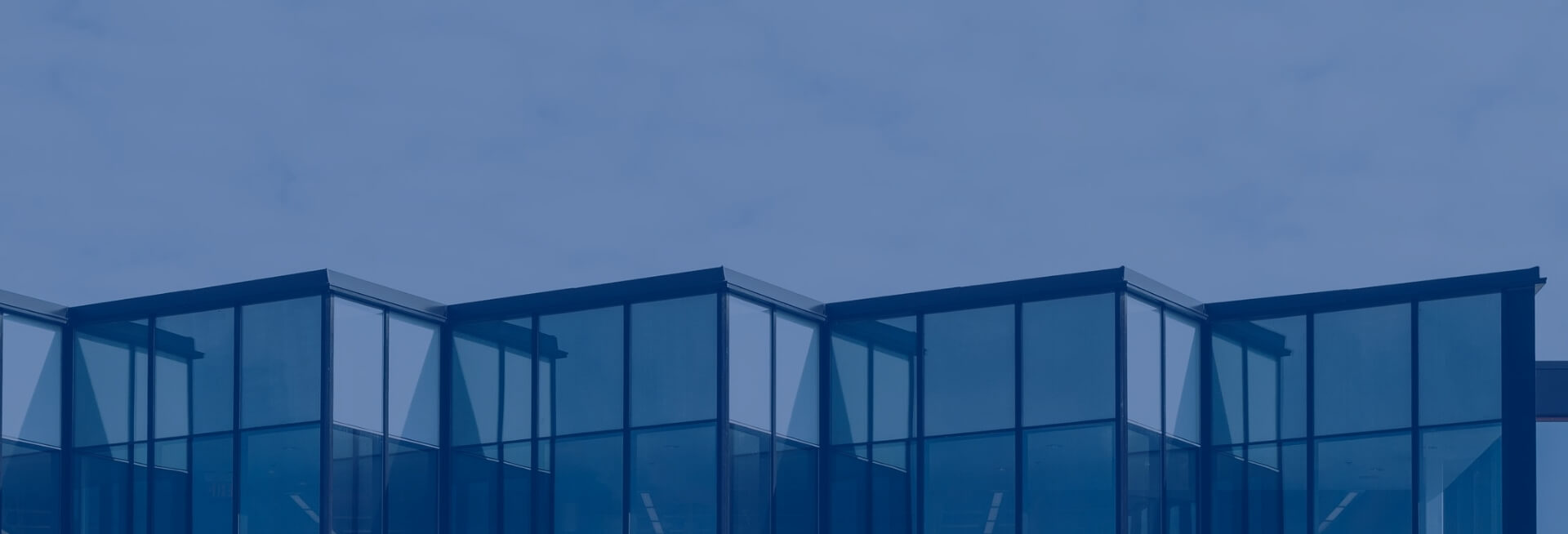
Get Started Now!
It takes less than a minute of your time. Or you may simply call +971 2 555 1 783