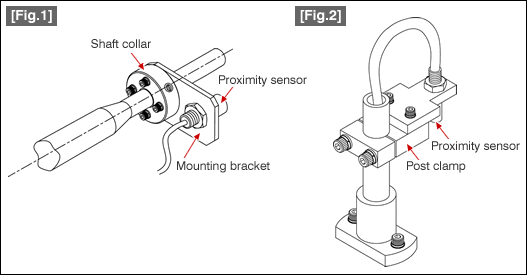
Vibration analysis is used to find out the vibration measurements of machines and are crucial to get the right detection, diagnostic performances, and sensor mounting. As a matter of fact, sensor mounting if not done correctly can greatly impact the quality of the time waveform. The type of mounting accessory used can significantly impact the measurement quality.
Thus, the settings of vibration measurement are crucial if you want to achieve the right detection and diagnostic performance. However, this is not the only thing to consider in order to achieve the desired objectives. For instance, the sensor mounting method to collect vibration data also has a significant impact on the quality of the time waveform.
Sensor Mounting as Basics of Vibration Analysis
It is a common practice that the sensor should be put as close to the machine as possible so that it may effectively sense and monitor the vibrations. The image shared below shows how closely the sensor should be mounted to the part that needs to be monitored.
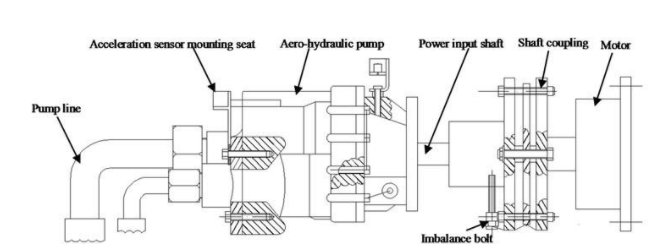
The Role of Mounting for Efficient Data Acquisition
When it comes to the aspect of data acquisition for vibration analysis, Sensor (Accelerometer) handling and mounting play an important role in the troubleshooting and analysis of a rotating equipment/ turbomachinery. Incorrect mounting may give readings that relate not only to a change in conditions but also to the instability of the sensor itself – hence making the input readings from the sensor unreliable. Hence, the correct mounting of a vibration sensor plays a vital role in the reliability of the analysis.
The sensors should be mounted as closely as possible to the load Zones, which is the bearing location in most cases. The closer you put your sensor to the machine, the better it senses the machine vibrations.
Accelerometers should be mounted onto a surface that is free from dirt and grease. The surface should be smooth, preferably unpainted, flat and larger than the base of the accelerometer itself.
Sensors should not be rocked to the machine casing instead care must be taken while mounting & removing the sensor.
The image below is indicative of the probable causes behind the vibrations that get captured by the sensor.
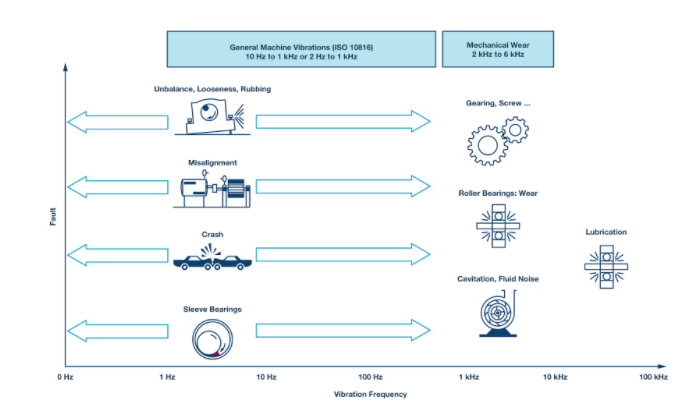
Sensor Mounting:
There are several mounting techniques used today based on industrial demands. Each kind is having its own pros and cons. We have to carefully select the type of mounting for onsite data collection based on our requirement. For example, Stud type sensor mounting gives the maximum frequency response than any other mounting techniques, but it is not practically possible to use stud type mounting in all the application other than permanent vibration monitoring.
Similarly, a probe tip may make it possible to reach a small or narrow area ̶ to obtain a measurement that nothing else can ̶ but is not be suitable to monitor high-frequency problems, such as bearings, cavitation and gear problems We have to wisely choose the type of mounting, understanding the requirements without compromising the quality of the acquired data.
The various mounting types and the sensitivity deviations are shown in the images below.
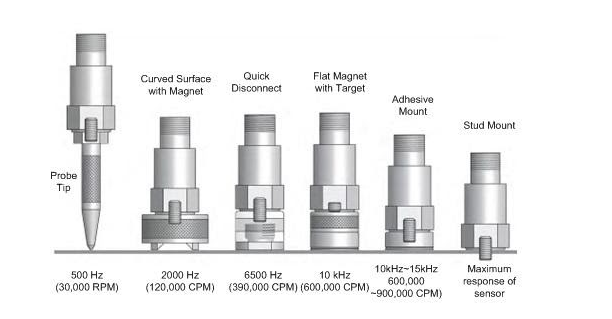
- Probe Type
- Curved surface with the magnet (2 pole magnet)
- Flat Magnet
- Adhesive Mounting Pad
- Adhesive Mount
- Stud Mount.
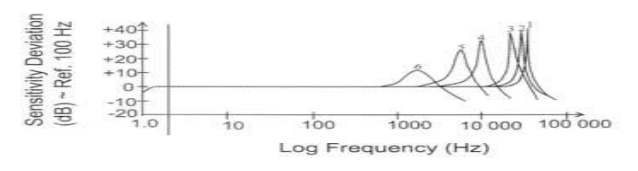
Types of Sensors:
Three Types of transducers used in industrial applications produce an electrical signal proportional to vibration amplitude.
- Proximity Probe- Displacement
- Velocity Probe- Velocity
- Accelerometer- Acceleration
Proximity Probe:
- Permanently installed on large machines.
- Measures relative displacement b/w the bearing housing and the shaft.
- Called Eddy Current Probe
- Frequency range 0 to 60,000 CPM
- Used 900 apart to display shaft orbit plot
Velocity Probe:
- Oldest of all
- Produces signal proportional to the velocity
- Self-generating and needs no conditioning electronics
- It is heavy, complex and expensive
- Frequency response from 600 CPM to 60,000CPM
- Temperature-sensitive
Accelerometer:
- Works based on the piezoelectric effect
- Produces signal proportional to the acceleration of the seismic mass
- Extremely linear amplitude sense
- Large Frequency range
- Smaller in size
Vibration Analysis Services from Technomax
Technomax offers reliable condition monitoring services like vibration analysis, infrared Thermography Testing, Light Survey, Lube Oil Analysis, Partial discharge Testing etc.
Learn More About Our Services
Recent Blogs
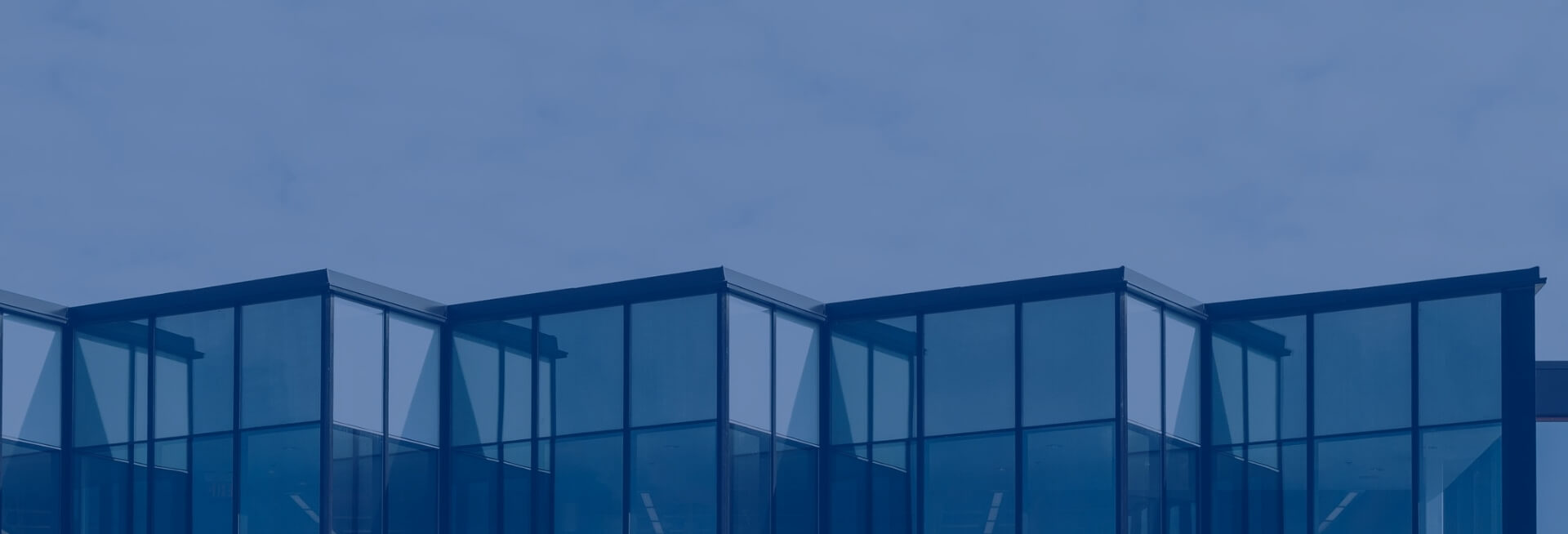
Get Started Now!
It takes less than a minute of your time. Or you may simply call +971 2 555 1 783