- Services
- Eddy Current Tube Inspection
Eddy Current Tube Inspection
Tubes are a common component in a lot of industrial equipment, and especially so for the oil and gas, chemical, nuclear, fertilizer, marine, air conditioning, and petrochemical industries. Inspecting heat exchanges is important, and necessitates precision as there can be hundreds of tubes, and the tiniest of circles that need to be examined. You can save a lot of time by detecting common problems like cracks both circumferential or longitudinal, pitting, corrosion, or changes to the exterior or interior surfaces of tubes. At Technomax, we can help you ensure that there are no delays due to abnormal tube function with our eddy current tube inspection services. We use state-of-the-art technology to inspect tubing applications and identify defects.
It must be noted however, that this type of testing is not suitable for ferrous material; it is good for titanium, steel or copper. At Technomax, we can also conduct remote field and magnetic biased eddy current tests of carbon tubing.
Intro
One of the most commonly used non-destructive methods to inspect tubing is eddy current testing. This can be used for tubing in various equipment like air coolers, condensers, steam generators, feedwater heaters, and heat exchangers.
Eddy current tube testing is an extremely specialized and delicate job that necessitates sophisticated tools and expertise. Our team of non-destructive testing inspectors are ASNT, NAS410 II/III level and PCN certified in this activity and have immense experience in performing these tests. Technomax can ensure that you get a precise evaluation of not just the present condition but also the expected life remaining for your tubing so that you can make informed decisions about the tubes’ integrity management.
Benefits
- It helps in detectinIt helps in detecting defects that are far-surface, near-surface, or surface breaking.g defects that are far-surface, near-surface, or surface breaking.
- It can differentiate between OD and ID defects.
- Eddy current tube inspection can detect cracks, large porosities, wear, corrosion, and other volumetric defects.
- In about 10 hours’ time, we can examine up to 700 tubes, each measuring 6 meters on average.
- We can perform this test in applications for different reasons, apart from detecting flaws
- The testing can be performed through coatings and paint. These are:
- a. Measuring thickness of coating
- b. Testing condenser tubes, wires etc.
- c. Detection of subsurface corrosion
- d. Inspecting bolt holes
- e. Inspection of corrosion under fireproofing and insulation – CUF and CUI
- f. Detecting surface cracks on aluminum alloys
- g. Detection of thinning or discontinuities of walls of tubes non-ferromagnetic in nature.
- h. Inspection can be conducted without the eddy current tube probes touching the part being inspected.
How is it done at Technomax
At Technomax we use electromagnetic induction to identify tubing flaws, by inserting a probe into the tube and making it travel its whole length. Our technicians send alternating current into the coil and this generates a round magnetic field around it. Then the probe’s electromagnetic coils generate eddy currents, and our team measures the probe’s electrical impedance. The defects in the tube are revealed through the information collected by the probe. The software records the scanned data, which we maintain to use as backup for the future.
- For air conditioner tubing applications, the technique differs slightly as the design of the equipment is different. Heat dissipation is achieved with the use of integral fins, which means they are vulnerable to circumferential cracking. Inspection becomes more difficult as the un-finned land area is used for inserting the bundle support plate. Hence eddy current tube bobbins are used to check the straight integral finned tube portion. However, they are not as effective in detecting circumferential cracks and at the support plates as the previous method. This happens because there is a huge variation in the liftoff which affects the probe’s signal significantly.
- At Technomax we use dedicated AC probes with best-in-class AC coil configuration made with study material, with probe heads that can be easily detached. With these new sensors we can identify circumferential cracks; thanks to the low variation in the liftoff, it can also detect cracks in tube sheet and support plate locations, giving data that is precise and reliable.
- Technomax has considerable experience in eddy current tube testing for different industries, and we understand that businesses need to get their equipment up and running as quickly as possible. Outages and downtimes hamper productivity, and this is why our technicians are trained to perform these inspections thoroughly in the shortest possible time. With zero compromise on quality, we provide some of the quickest eddy current tube inspection services.
Other Services & Products
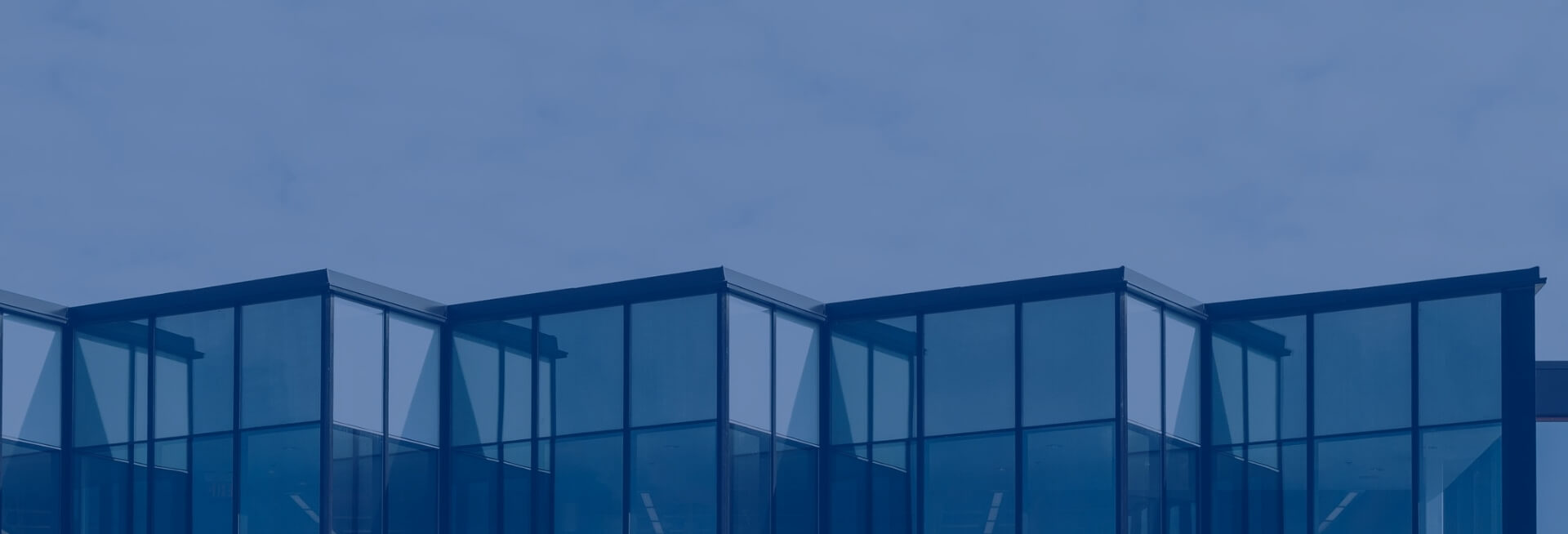
Get Started Now!
It takes less than a minute of your time. Or you may simply call +971 2 555 1 783