- Services
- Infrared Thermography Testing & Analysis
Infrared Thermography Testing & Analysis
Infrared thermography testing is a non-destructive and non-intrusive testing process employed as a predictive maintenance inspection technique to detect abnormal heat patterns in machines. A device known as a thermal imager is used in this method to detect radiation emitted from an object, converting it to a temperature and creating an image of the detected temperature distribution, known as a thermogram. The thermograms are utilised to analyse the thermal anomalies in different types of equipment. Being the leading engineering company in UAE, Technomax offers unrivalled Infrared Thermography Services in UAE & Middle East across various industries.
Our well-trained and experienced team skillfully interprets thermograms to see what is invisible to the naked eye and detect hotspots, heat loss, leaks, insulation problems, and other abnormalities in machines. Technomax’s thermal imaging technology is a reliable, cost-effective, and efficacious way to predict the trouble ahead and facilitates our clients to keep their plants up and running by avoiding unplanned downtime and unforeseen repair costs.
Applications of Infrared Thermography Testing at Technomax
Technomax utilises thermal imaging to detect a variety of fault conditions before they become a catastrophic concern to people and property. The infrared thermography (IRT) inspections we offer are beneficial for various fields including, but not limited to:
- Electrical Systems: IRT assists in finding faulty electrical or overloaded circuits in various electrical systems.
- Mechanical Systems: Bearing failures, improper belt tension, misalignment of coupled equipment, abnormal warm motors, etc., in mechanical equipment can be detected by thermal imaging.
- Fluid Systems: Faults like line blockages, tank levels and pipe or fluid temperatures can be identified at the earliest stage.
- Construction: Building diagnostics leverages thermal imaging to identify insulation defects, moisture problems, plumbing flaws, air leakage, etc.
- Low-Slope Roofs: IR thermography aids in monitoring roof conditions and detecting wet roof insulation.
There are numerous applications for Infrared thermography testing:
1. Test and Measurement
The use of infrared cameras, infrared thermometers, pyrometers, etc. has been extensively used by research scholars to measure the temperature of individual particles in coal combustion reactors, to initiate an endeavor to understand the transient phenomenon behind combusting particles.
2. Injection Molding
To measure the temperature of the surface of the distribution products, the thermal imager is used through an online system.
3. Manufacturing
In the metal manufacturing industry, it is crucial to monitor the temperature of the molten metals to ensure that the process temperature is adequately maintained at the casting level.
4. Condition Monitoring
To maintain the overall health of the equipment and avoid any sudden damage or disruption in the production process, a thermal imaging camera is the most coveted technology for condition monitoring services. It can be used to detect catastrophic failure of the equipment or manufacturing process. It is also a cost effective method.
What is Thermography Testing?
Thermography testing is the process of testing components using an infrared camera to look for abnormally hot or cold areas operating under normal conditions. It is a viable non-destructive evaluation technique for the characterization of corrosion in metallic materials and is the simplest of all thermal inspection techniques.
In addition, it can be used to check for fouling or internal plugging of piping systems and to check the quality of refractory linings. It can also be used for leak detection, composition changes, and disbonds in laminates. Using thermography, the temperature of objects can be made visible.
Infrared Thermography Testing Procedure
Any object with a temperature above −273.15 degrees Celsius (absolute zero or 0 kelvin) emits thermal infrared energy, which is undetectable by the human eye. Technomax’s thermal imaging technique uses advanced thermal image scanners to detect and display these infrared wavelengths regardless of visible illumination. An abnormal temperature pattern typically precedes equipment failures, corroded electrical connections, damaged components, etc. Our trained and experienced thermographers can easily monitor the thermal performance and localise the flaws and faulty conditions in equipment and industrial processes under normal operating conditions by analysing the thermograms.
Through interpreting the thermal asymmetries, Technomax can detect defects ahead, identify the root causes, and correct the problems, saving the plant from possible system failure or performance issues. Being the leading provider of IR thermography services, we solely use the best thermal imaging equipment available in the industry, ensuring trustworthy and precise real-time results without interruption in an ongoing process.
Benefits of Infrared Thermography Testing
Routine IR thermography inspections by Technomax’s expert personnel provide a myriad of advantages and the benefits of infrared thermography includes:
- The process is non-invasive, non-destructive, and cost-effective
- It can be used in condition monitoring
- Identifies problems in the equipment or device before they occur
- Prevents loss of production due to unexpected breakdowns
- Reduces unscheduled downtime
- Significant savings in money and time
- Keeps repair and maintenance costs down
- Extends the useful life of the machine assets
- Reduced spare parts inventory base
- Enhances product quality & consistency
Why Choose Our Infrared Thermography Services?
Are you looking for the best Infrared Thermography Testing providers in the Middle East to conduct regular thermography inspections and get the most out of the survey? Then, look no further than Technomax, the market leader in providing various infrared thermography services in the UAE across a wide range of industries. Our accredited and trained team holds expertise in finding unnatural temperature distributions and their underlying causes using industry-leading thermal imaging equipment. Thereby, we detect faults in time and offer sustainable solutions to rectify the infrared thermography problems that come under the condition monitoring services.
Our IRT services as a non-contact and non-invasive condition monitoring tool facilitate the timely resolution of defects through the early detection of flaws. Over a decade’s experience in this sector has enabled us to emerge as the top name in providing dependable, accurate and less expensive thermal imaging services. Contact us now to find out the anomalies in the equipment before they become costly distress for your business.
Other Services & Products
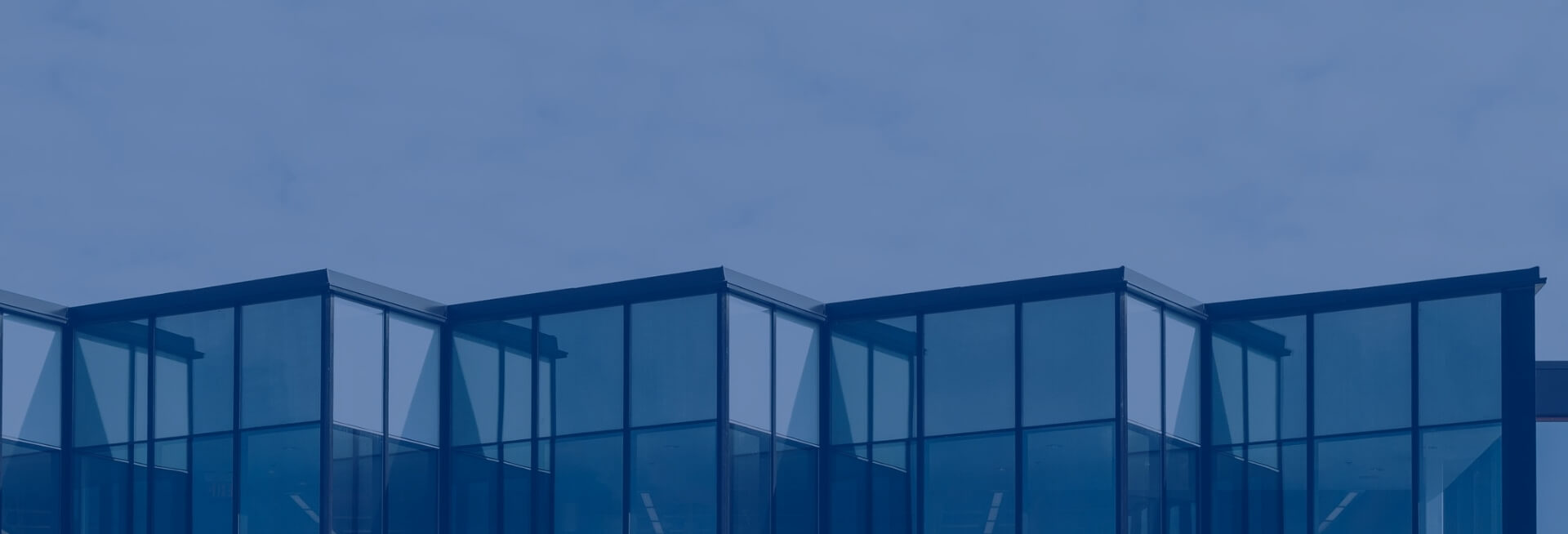
Get Started Now!
It takes less than a minute of your time. Or you may simply call +971 2 555 1 783