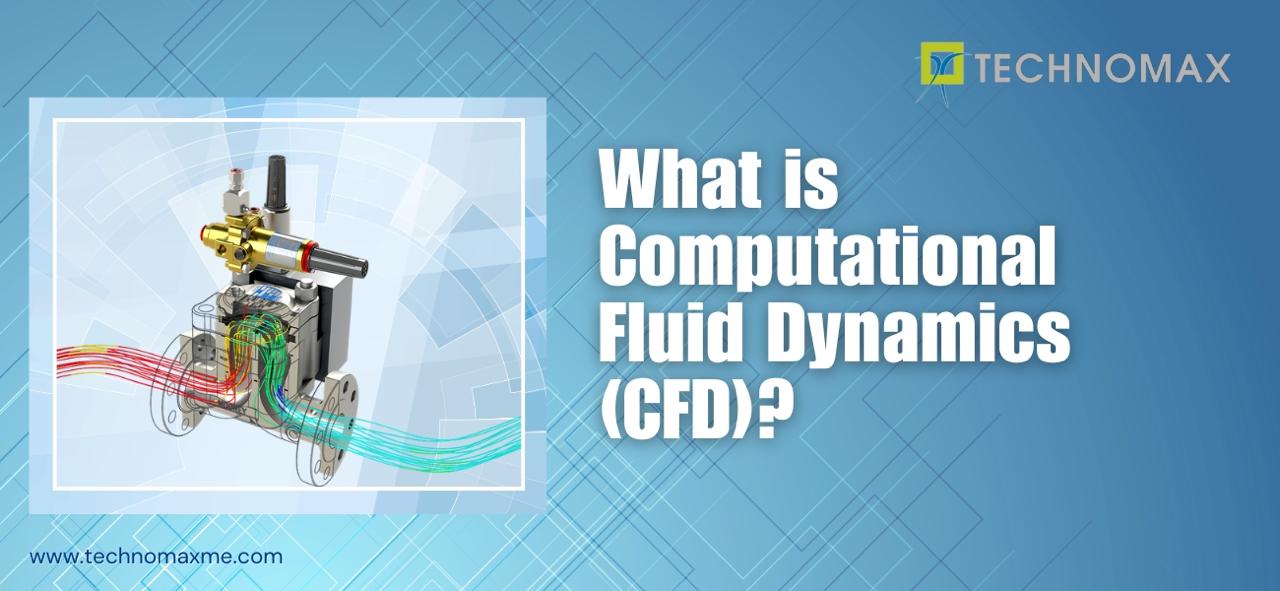
What is CFD Analysis(Computational Fluid Dynamics)?
CFD Analysis (Computational fluid dynamics) is a technique that adopts numerical analysis and computer simulations to study the physical behaviour of fluids in a system, over time. The method helps us understand how the fluids move and how their properties change in response to external forces or conditions, using analysis-generated visuals and graphs.
Computational fluid dynamics (CFD) is a branch of fluid mechanics that uses computerized techniques to analyze and understand the behavior of liquids and gases (fluids) when they move or interact with external forces within a system.
CFD modeling and analysis are popular as they solve real-world fluid flow and heat transfer problems more efficiently than any other traditional prototype-based physical testing methods.
For example, in HVAC units like ducts, CFD analysis is conducted to predict and optimize the airflow within the system, without depending on conventional physical test methods.
These variations are measured in terms of fluid properties like velocity, pressure, temperature, and heat transfer, which in turn are determined by a set of mathematical equations derived from fundamental laws of physics. This includes the laws of conservation of mass, momentum, and energy.
How CFD Analysis(Computational Fluid Dynamics) Works?
CFD analysis is performed using specialized CFD software, where the desired model is created and simulated. A CFD analyst uses these tools to simulate and analyze the fluid flow based on its physical conditions, and predict the behaviour of the fluid on a product or a system.
The process involves creating the geometry of the model and dividing it into a mesh of small cells. The fundamental equations of CFD are applied to each cell to determine the properties. Since the number of cells is large, these equations are solved using numerical techniques, which are inbuilt within the software.
To perform the analysis, fluid properties and boundary conditions are provided as input. Based on these, the software conducts recurrent calculations until the solution becomes stable.
The final analysis results provide a detailed overview of how the velocity, pressure, and temperature change throughout the system. The results are compared with the design standards for validation, to detect inefficiencies and improve overall performance.
Application of CFD Analysis in Various Industries
CFD is used where it is essential to predict fluid flow, heat transfer, or fluid-structure interaction. It is widely applied in the areas of:
- Aviation: To optimize aircraft and missile aerodynamics, engine performance, and stability analysis.
- Construction: To analyze wind loads on buildings, tunnel airflow, pollution dispersion, etc.
- Automotives: To predict and optimize engine combustion, ventilation, and most importantly, vehicle aerodynamics.
- Chemical Industries: To study multiphase flows, cavitation in reactors and pipelines.
- Healthcare: To study the fluid flow in the human body, airflow through the respiratory system, and evaluate the efficiency of new medications
- Energy Production: To enhance the design and performance of the boiler, turbine, fuel cell, etc.
Equations Used in CFD Analysis
In CFD analysis, the fluid medium is studied using simulations and mathematical calculations based on partial differential equations. These equations represent three fundamental laws of physics:
- The law of conservation of Mass
- The law of conservation of momentum
- The law of conservation of energy
1. Law of Conservation of Mass or Continuity Equation
The law of conservation of mass states that the total mass of a fluid in a closed system remains constant over time- it can neither be created nor destroyed. In fluid mechanics, this principle is expressed as the continuity equation:
Where ρ is the density and u is the velocity of the fluid.
2. The Law of Conservation of Momentum or Navier-Stokes Equation
The law of conservation of momentum states that the rate of change of momentum of a fluid volume is equal to the sum of the forces acting on it. The principle is expressed by the Navier-Stokes equation:
Where p is the pressure, μ is the viscosity. The left-hand side represents the rate of change of momentum, and the right-hand side sums up all the forces acting on the fluid.
3. The Law of Conservation of Energy or The First Law of Thermodynamics
The law of conservation of energy states that the change in the total energy of a fluid or a system must be equal to the energy added or removed from the system. The energy equation can be represented as:
Here, dQ is the heat added to the system, dW is the work done on the system, and dEt is the increment in the total energy of the system. One of the commonly used energy equations in CFD analysis is:
Here, ‘h’ is enthalpy, ‘T’ is the temperature, ‘k’ is the thermal conductivity, and φ represents viscous dissipation or internal heat generation.
Based on whether the fluid is compressible or incompressible ( density constant; ∂ρ/∂t=0), the three unknowns velocity u, pressure p, and temperature T are determined simultaneously.
Why is CFD Analysis Important?
As the demand for high-performing products intensifies, it's imperative to shorten their development cycles. Only online simulation techniques like CFD offer a game-changing advantage by providing:
- In-depth insight into fluid behaviour
- Design optimization and innovation
- Visual clarity and non-intrusive testing
- Faster time to market
- Cost reduction
- Risk mitigation
CFD Software Used for Analysis
Popular software that offers computational fluid dynamics (CFD) analysis includes:
- ANSYS Fluent
- STAR-CCM
- Autodesk CFD
- OpenFOAM
Steps in the CFD Process
The general process followed for CFD analysis includes
- Model generation: Create a 3D geometry of the physical element using CAD or similar software and import it into the CFD software.
- Defining fluid domain: Specify the fluid region and properties, type of flow, and whether it is moving internally or externally.
- Setting boundary conditions: Specify how fluid enters, exits, and interacts with the surfaces.
- Analysis: Steady or transient simulation is performed based on system behaviour.
- Result evaluation: Analyze velocity, pressure, and temperature through visual outputs.
- Optimize the system: Use the CFD insights to refine and improve performance without physical testing.
How Technomax Perform CFD Analysis
- Multiphase Flow Simulation – Computational modelling of phase interactions (liquid-liquid, gas-liquid, or solid-fluid) to optimize separation processes, mixing efficiency, and equipment performance in industries like oil & gas and chemical processing.
- HVAC Flow Dynamics – CFD-driven analysis of airflow, thermal stratification, and smoke propagation to optimize ventilation, thermal comfort, and fire safety in residential, commercial, and industrial environments.
- Process Flow Optimization – Predicting fluid transport behaviour, pressure losses, and mixing efficiency to enhance pipeline hydraulics, reactor performance, and industrial process reliability.
- Aerodynamic Performance Assessment – Simulating external and internal flows to quantify drag, lift, and pressure distributions for optimizing vehicle aerodynamics, aircraft stability, and wind-exposed structures.
- Turbomachinery Flow Analysis – High-fidelity CFD evaluation of blade aerodynamics, secondary flows, and efficiency losses in compressors, turbines, pumps, and fans to enhance performance and durability.
- Thermal Management Engineering – Analysing heat transfer mechanisms, cooling efficiency, and thermal gradients to improve component reliability in industrial cooling systems and electronic enclosures.
- Electronics Thermal Regulation – Modelling conduction, convection, and radiation effects in PCBs, heat sinks, and power modules to prevent thermal failure and optimize electronic system longevity.
At TECHNOMAX, we provide data-driven insights and tailored solutions, helping industries achieve superior efficiency, safety, and performance. Contact us today to explore how CFD can optimize your systems.
CFD Analysis Services with Technomax
Achieving accurate results from CFD analysis not only requires robust software but also a strong practical engineering experience. Technomax offers end-to-end CFD analysis services starting from CAD modeling and CFD simulation to validating performance and refining designs by skilled and experienced CFD specialists.
Delivering data-driven insights facilitates industries to achieve superior efficiency, safety, and performance through specialized services such as aerodynamic assessment, multiphase flow analysis, thermal management, and HVAC simulation.
We also provide condition monitoring services like vibration analysis, laser shaft alignment, infrared thermography testing and more in UAE and Middle East.
Looking for expert CFD analysis services in UAE and Middle East? Partner with Technomax to gain precise insights into fluid behavior and system performance. Contact us today for a tailored solution!
FAQs
1. What is meant by CFD analysis?
Computational fluid dynamics (CFD) is defined as a technique that adopts numerical analysis and computer simulations to study the physical behaviour of fluids in a system, over time.
2. What does a CFD analyst do?
A CFD analyst uses these tools to simulate and analyze the fluid flow based on its physical conditions, and predict the behaviour of the fluid on a product or system.
3. What are CFDs used for?
Computational fluid dynamics (CFD) is used to simulate and analyze fluid flow and heat transfer to help engineers optimize system performance, predict physical behaviour, and solve complex flow problems in various engineering applications.
4. How to analyse a CFD?
CFD analysis results provide a detailed overview of how the velocity, pressure, and temperature of the fluid change when it passes through a product or a system. The results are compared with the design standards for validation, to detect inefficiencies and improve overall performance.
Learn More About Our Services
Recent Blogs
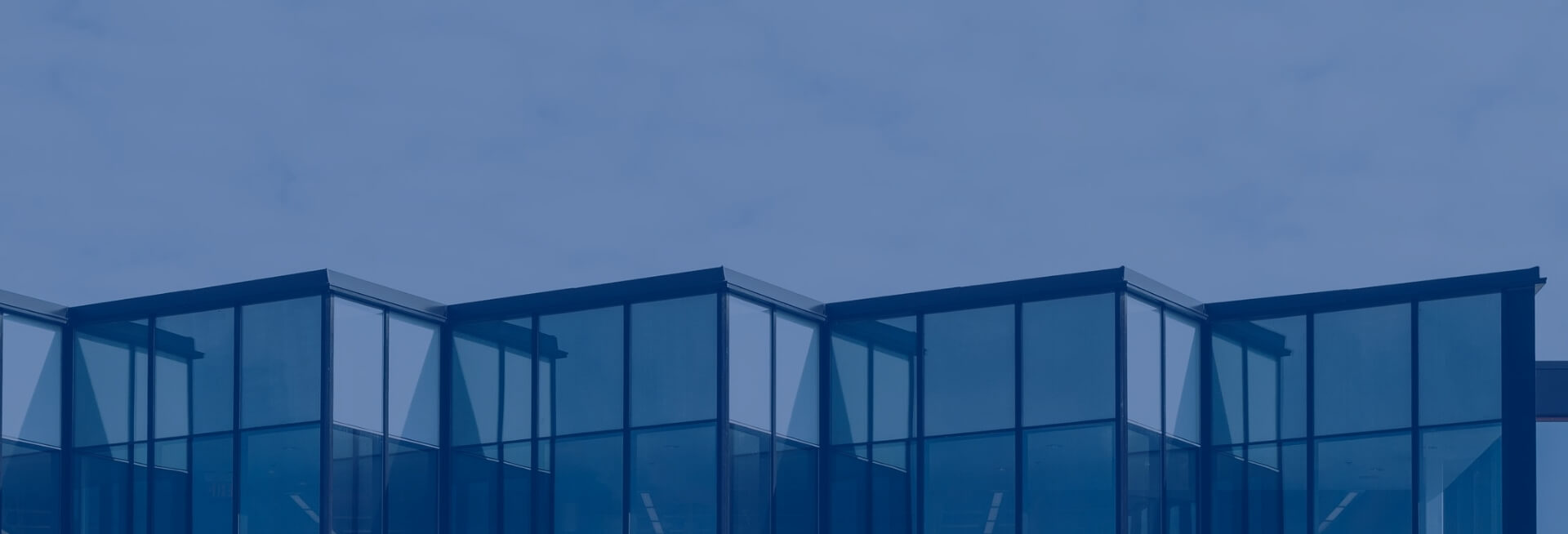
Get Started Now!
It takes less than a minute of your time. Or you may simply call +971 2 555 1 783