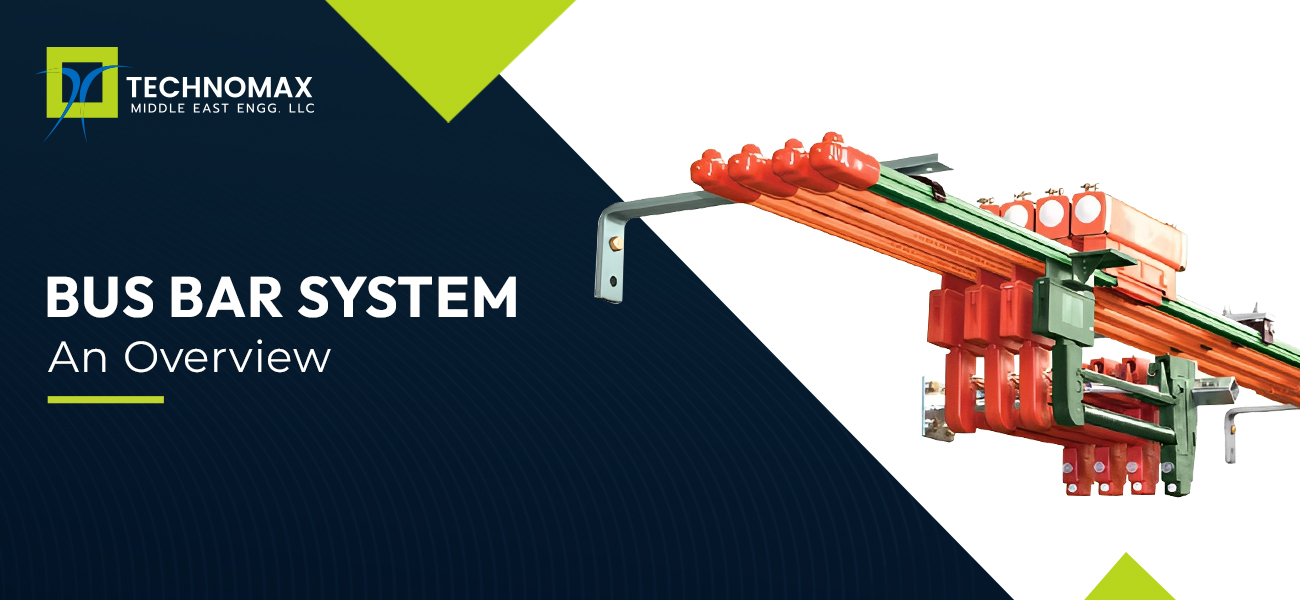
Busbar Systems are essential for every power application that provides major interfaces between the outer world and the power modules. It has been witnessed throughout the design iterations in industrial cranes that occurred in recent years with the evolution of industries. Conducting sufficient amounts of currents in the applications, busbars are mandatory with a focus on electrical power distribution in cranes while meeting the dynamic application needs. In this blog, let's deep dive into everything about electrical bus bars, types, and their applications in detail.
What Are Busbars?
An electrical busbar or a conductor bus bar, as the name suggests, defines a conductor or the aggregate of conductors that receive electric power from the incoming feeders, to further distribute it to outgoing feeders. Otherwise, an electrical bus bar is an electrical junction where the incoming and outgoing currents meet. The conductor busbar systems gathers electrical power in a centralized location.
DSL Busbars are made up of highly electrically conductive metals and they distribute & carry power from a source to a destination or multiple destinations. They are used in EOT Cranes to supply power from the grid to the crane control panel. The full Form of the DSL busbar is Down Shop Lead.
You may also like to read:
- Crane Electrification – Bus Bar vs. Festoon System
- Anti-Collision Systems in EOT Cranes
- Key factors to check when sourcing for EOT cranes
How Do Busbars Work?
Busbars are usually used to connect electrical power sources and loads. It connects the generator and main transformer in power busbar systems and also interlinks the incoming/outgoing transmission lines. The busbar is visibly a copper or aluminium strip that transfers electricity in a substation, electrical apparatus, or switchboards. The flexible bus bars are made using aluminum tubes with disc insulator strings on either side and gantries to support them. While rigid busbars get support on post insulators and are made using Aluminum tubes. The size of the bus bars determines the amount of current it can carry safely. The common shapes are flat strips, hollow times, etc. since these shapes can allow more heat dissipation of the large ratio of surface area to cross-section area.
The Function of a Bus Bar
A bus bar serves as an electrical connection point where it gathers electric power from incoming feeders and then disperses it to outgoing feeders. The primary function of a bus bar is to transport and distribute electricity, contributing to the efficiency of systems. In complex electrical setups, busbars can be a highly effective solution.
Nature of Busbar Connection
Busbars could be supported in two ways: either on insulators or the insulation to surround them. A metal earthed enclosure busbar connector safeguards them against accidental contact. Neutral busbars also need insulation. Busbars could be also enclosed in the metal housing which uses bus-duct, isolated phase bus, or busway segregated phase bus. Connecting the busbars and the electrical apparatus needs welded connections or bolted clamps.
How Are Busbars Rated?
Rated current- This is the RMS measure of current that busbars can conduct persistently with the rise in temperature within a particular limit.
Rated voltage- This is the RMS voltage value between lines for which you need the busbar
Rated frequency- The value of frequency for which the busbar systems work
Rated short-time current- The RMS current value that bus bars carry for specified temperature rises in a specified duration
Rated insulation level- the normal rated voltage, power frequency withstand voltage, switching impulse voltage or lightning impulse withstand voltage used to characterize the insulation levels.
Factors to Consider While Selecting Busbars
You need to consider certain factors before choosing the busbar sizes—these include current carrying capacity, surface gradient, performance, etc. Electrical and mechanical stresses like short circuit fault currents should be considered to withstand thermal stresses. Also, the short circuit effects that cause stress to the clamps and connectors need to be well addressed. Let's check out the factors considered in selecting bars factors:
- Ambient temperature
- Operating temperature
- Height from sea level
- Voltage level
- Short circuit current
- Type of bar coverage
- The number of busbars in each phase is considered.
Types Of BusBar Arrangements in Power System
Let’s now take a glance at the various types of busbar systems and learn more about them:
- Single Busbar System
This system arrangement consists of a main bus that remains energized every time and every circuit is connected to this. This arrangement offers the least amount of dependability. The complete loss of the substation can occur with the bus faults or any failure in the operation of the circuit breaker.
Advantages:
- Cost-effective
- Needs small area
- Highly expandable
- Easy Concept and operation
- Great on protective relaying application
Disadvantages:
- Minimal reliability
- Failure in the circuit breaker can cause loss of the whole substation
- Complicated maintenance switching which disables certain protective relay systems
- Sectionalized Busbar Systems
This is an extension of a single busbar arrangement; however, it comprises two or more single bus systems where each of them gets tied with sectionalized breakers. The breakers can function open or closed based on the system requirements. In case a failure in the breaker or bus fault occurs, the bus section affected can be removed which prevents the substation from shutdown.
Advantages:
- Flexible operations
- Greater reliability compared to a single busbar system
- Bus fault or breaker failure affects only a part of a substation
Disadvantages:
- Costly than single bus scheme
- Sectionalizing needs additional circuit breakers
- Sectionalizing results in circuit faults
- Main & Transfer Busbar Systems
This system comprises two independent buses where the main bus is usually energized in normal operating conditions. Every incoming and outgoing circuit is fed using circuit breakers and switches from the main bus. In case the circuit breaker needs repair, the integrity of circuit operation can be managed with bypass and bus tie equipment.
Advantages:
- Can be expanded easily
- Reasonable cost
- Requires small land area
Disadvantages:
- The bus tie needs an additional circuit breaker
- Bus fault can cause a loss in the whole substation
- Complicated switching essential to remove circuit breaker from service for the maintenance
- Ring Bus Systems
This refers to an added extension of the sectionalized bus systems — it uses the interconnection of two open ends of bus bars, using another sectionalizing breaker. This results in a ring or closed loop with every bus section separated by a circuit breaker. For high operational flexibility and reliability, each section should supply only a single circuit. If a fault happens in the bus or circuit breaker, only the limited circuit will be eliminated.
Advantages:
- Maintenance of a circuit breaker can be done without power interruption
- Offers a redundant path to the circuit in case of failure
Disadvantages:
- Bit difficult to add a new circuit line
- Breaker and A-Half Busbar Systems
In this configuration, two main buses are usually energized with three circuit breakers electrically connected between the buses. In such an arrangement, three circuit breakers are utilized for two separate circuits, where the circuit breaker can be eliminated without affecting any circuits.
Advantages:
- High reliability
- Flexible functionality
- Double feed to every circuit
- Bus faults don't impact the service of the circuit
- Every switching is done with a circuit breaker
Disadvantages:
- Every circuit needs a separate potential circuit for relaying
- Double Breaker Double Bus System
In this configuration, two main buses and two circuit breakers are utilized to connect the buses. The two circuit breakers electrically connect the buses to limit, and these systems are generally used in large generating stations due to the high-cost concerns.
Advantages:
- Operations are flexible and reliable
- Switching using circuit breakers
- Only one circuit loss even during breaker failure
Disadvantages:
- Expensive
- Two circuit breakers are required for every circuit
Busbar Systems for Crane Electrification
Bus bars are the most secure, economical, and easy-to-maintain solutions for enabling crane electrification. With busbar systems, you minimize the system costs, enhance reliability, improve capacitance, and prevent all sorts of wiring errors. A wide range of conductor busbar cables is accessible for industries to conduct safe crane electrification with low maintenance risks.
To Conclude
Busbar systems are a major factor behind carrying current between sophisticated power applications and assemblies. Installation and maintenance of busbar technologies require partnering with experts who can offer a wide range of implementation options. Working with these specialists can help you get advice on the various approaches to choosing the best technology and strategies to ramp up the product launch phases. To get the consultation and recommendations from the specialists at Technomax, a leading engineering company in UAE, and get perfect crane electrification solutions for your industrial cranes, get in touch with us today!
Learn More About Our Services
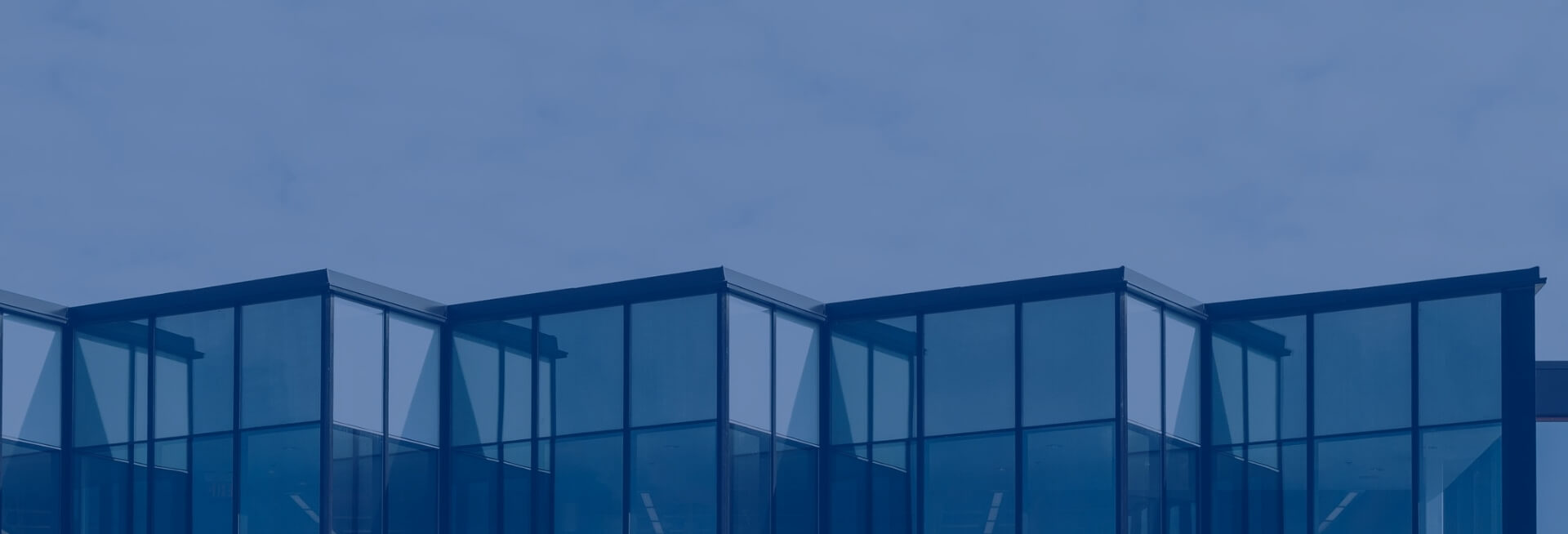
Get Started Now!
It takes less than a minute of your time. Or you may simply call +971 2 555 1 783